- Types of supply chain risks - The foundation of risk management for supply chain
- Known and unknown supply chain risks
- External and internal supply chain risks
- Supply chain risk management best practices
- 1. Prioritization of business continuity plan
- 2. Proactive supplier risk management
- 3.Improve cyber supply chain risk
- 4. Management of environmental risks
- 5. Track freight carrier metrics
- 6. Model risk event situations
- 7. Invest in a supply chain software firm
- Parting notes
In the last few years, a number of businesses have gotten affected by the unpredictable vulnerabilities in the supply chain. What it led to is recalls costing over millions for industries ranging from consumer goods, automotive to pharmaceuticals. The worst part of these supply chain disruptions can be seen in both government and private organizations struggling with cybersecurity breaches and the loss of key intellectual properties due to the lack of supply chain risk management practices.
While accepting, accessing, and mitigating supply risk has always been a part of the business domain, running a successful business in the present market structure is more challenging than ever before. The Covid-19 pandemic sent waves of volatility throughout every market, making businesses aggressively reform their operations, marketing, and supply chain operations.
Likewise, climate change implications like Amazon Rainforest fires have also caused a cascading chain of material loss, international political conflict, and human rights violations.
On the political front, the Ukraine-Russia war is causing its own set of disruptions in the supply chain industry. According to a Dun & Bradstreet report, over 374,000 global businesses depend on Russian suppliers – 90% of whom are based in the US About 241,000 businesses rely on Ukrainian suppliers of whom 93% are based in the US.
In such volatile and complex socio-political environments, the definition of what is supply chain risk management has changed. What once used to be around a certain set of use cases has today been extended to cover a range of internal, external and unknown, known sets of risks.
The correct supply chain risk management plan starts with understanding the kind of risks that a supply chain circle can encounter.
Types of supply chain risks – The foundation of risk management for supply chain
On an end-to-end level, every part of the global supply chain comes with some extent of risks affecting your company’s performance, reputation, and the bottom line. When left unattended, both external, internal risks and known, unknown risks can lead to serious damage.
Let us look at what the two categories of risks entail before we look into the best ways to handle supply chain risk management.
Known and unknown supply chain risks
Known risks are the ones that are possible to measure and manage over time. For example, a supplier’s bankruptcy causing disruption in the supply chain is a known risk. Likewise, risks around cybersecurity vulnerabilities can also be measured through supply chain risk management software analyzing the IT system inside-out.
Unknown risks are the ones that are impossible to predict. These can be climate change like a dormant volcano erupting and disrupting the supplier network, a cybersecurity attack that originated from deep inside the firmware of an electronic component. When it comes to supply risk mitigation, these pose the biggest challenge.
External and internal supply chain risks
External supply chain risks are the risks that come from outside your company. The absence of transparency makes it difficult for them to be anticipated, and they would need more talent, time, and resources when it comes to mitigation. Supply chain risk analysis is most difficult in the case of external risks.
The types of risks that fall under the external supply chain category are:
- Material risk – These happen when the material or finished goods do not reach the end-users. These risks can delay or stop operations altogether for the resellers of the goods.
- Demand risk – These happen because of poorly defined demand calculations, the demand-based risks leads to the excess product being made or, in contrast, unavailability of products to meet the demands.
- Business risk – These are caused by a change in suppliers’ organization structure, unanticipated sales to another company, etc.
- Environmental risk – These happen from several socio political issues, climate issues, and global health concerns. These risks are known to create devastating disruptions at different vulnerable points in the supply chain.
Internal supply chain risks emerge from inside the organization. With the right set of supply chain risk management processes, these can be easily mitigated and addressed. Since they are the most predictable out of all the risks, businesses have to keep an eye on their proactive management and mitigation to prevent them from happening.
The types of risks that fall under the internal supply chain category are:
- Manufacturing risks: These risks arise with the possibility of disruption in a key step or component in the workflow, which causes the operations to get off schedule.
- Business risks: These are the outcome of disruptions in processes around personnel, reporting, management, and other key business operations.
- Planning and control risks: These are caused by incorrect assessment and forecasting of planned production and handling.
- Mitigation and contingency risks: These risks can happen when a business does not have the right set of contingency plans in place for handling supply chain disruptions.
Now that we have looked into the different risks that need stringent supply chain risk management strategies, it is time to get down to those plans and look at how the instances of supply chain disruption can be lowered.
Supply chain risk management best practices
When we talk about risk management for the supply chain, the solution has to be very wide and highly proactive in nature. Moreover, it has to be designed for mitigating the risks in almost real-time after the disruption has occurred.
Let us look into some of the supply chain assessment and mitigation strategies we share with our clients when they contact us for a solution.
1. Prioritization of business continuity plan
An effective supply chain risk management practice is as much about mitigation as it is about prevention. Protection of a company’s ability when it comes to maintaining the operations in the middle of a supply chain disruption is where a business continuity plan comes into the picture.
Achieving this calls for a comprehensive risk assessment. Identification of all the different risks can help create a list of failure points in the supply chain, helping businesses create protocols and plans around mitigation. A way of approaching this lies in the PPRR model (Prevention, Preparedness, Response, and Recovery).
- Prevention – measures taken for reducing and eliminating risk exposure in the supply chain
- Preparedness – measures around establishing appropriate, time-sensitive responses
- Response – controlling, limiting, and minimizing the impact of the supply chain disruption
- Recovery – measures taken to overcome disruptions quickly and safely
2. Proactive supplier risk management
Businesses won’t be able to perform supply chain risk analysis and management effectively until they get visibility of the risks around the suppliers. You should conduct a thorough supplier risk assessment to identify and eliminate risk exposures built by supplier behavior and the many facets of the third-party relationships. Performing these external supply chain assessments should be a part of a regular supplier relationship management strategy conducted by a focused cross-function IT risk management team.
The results of these assessments should be used by the risk management team for creating a vendor risk management program. A program that would prepare your business against every risk that arrives from the supplier network. Moreover, the data can be used for creating redundancies and minimizing the supply chain blockages.
3.Improve cyber supply chain risk
In the digital age, where supply chains use modern technologies for more key business processes, cyber risks are bound to happen. When merged with other process gaps in the supply chain, these can lead to massive disruptions in the process.
The solution to these risks can be seen in:
- Establishing a compliance standard for all the third-party vendors
- Defining the role of users and restricting the ability to access the system
- Performing an in-depth vendor risk assessment before signing any contract
- Developing a disaster recovery plan for instances where the breach has happened
- Regular updation of company’s antivirus and firewall software solutions
4. Management of environmental risks
The Covid-19 pandemic has exposed the gaps that were always there in the global supply chain network. Now, although there is no definite way to prepare for environmental risks, it is important to build a supply chain risk management plan to ensure that your business continuity goes on.
There are a few strategies you can apply when it comes to managing environmental risks:
- Multisource – You should categorize the suppliers not just on the basis of costs but also the impact of disruption. The ebay approach would be looking for a supplier that works out of multiple locations.
- Nearshore – You should look for suppliers close to your center of operation and endpoint of the supply chain to lower the product development and delivery time. Now, although it can be expensive to partner with regional suppliers, it can be helpful when it comes to saving the potential risks.
- Build buffer – With an expensive approach, creating a buffer comes in handy when doing new product launches or expanding in new areas. It doesn’t just lower the climate-driven environment risk but also helps with stockpiling goods that are always in demand.
5. Track freight carrier metrics
In order to build trust among the stakeholders, it is important for manufacturers to establish a dependable delivery timeline. While it is important that you partner with the best freight carrier provider to deliver consistent results, it might not always happen.
A crucial part of managing risk in the supply chain will also lie in evaluating your carrier. Here are the things you should keep track of to prevent any supply chain disruption –
- Transit time
- Number of stops and their average duration
- Average loading time
- Optimization of route
- Maintenance schedule
6. Model risk event situations
Imagine if you get the ability to predict the risk event before it happens. While technology is not developed to that extent yet, facilities like predictive analysis, data science, and data modeling bring us very close to making it happen. These advanced technologies can be used to build models of potential risk scenarios driven by the worst cases.
When you have access to these intelligent risk models, you are able to identify the gaps and prepare your business for the time when the disaster will happen.
7. Invest in a supply chain software firm
Managing supply chain risks in the modern, digital age calls for advanced analytics and artificial intelligence that would complement human’s ingenuity. You would need supply chain risk management software that is decentralized and high on the transparency factor, while being augmented by technologies like machine learning and robotic process automation. While it has been established that risks are a part of the supply chain business, what is scary is that there are businesses which still don’t have a supply chain risk management software in place.
These software that a supply chain focused enterprise custom software development firm creates would offer a range of benefits like:
- Elimination of human delays and errors
- Real-time, decentralized data management and risk monitoring across the entire supplier network
- Simplification of data analysis that transforms data into risk models, contingency plan, and process improvement modes
- Automatic, cloud-driven backups accessible from around the globe in real-time
These are only surface-level benefits that a supply chain risk management software can get you. A well-planned and executed software can help with both proactive and preventive mode of handling supply chain risks.
Parting notes
The extent at which the global supply chain has grown has made the sector irreversible. And with them, the risks of the supply chain at a global scale have also become irreversible.
In our extensive experience around building software for risk management for the supply chain, we understand that it is crucial for organizations to create robust programs for the management of both known and unknown global supply chain issues. The need for proper supply chain risk management has grown to a level of urgency where the business leaders should not just set governance models and processes, but also bring about a change in company-wide mindset.
By adopting the approaches that we have mentioned here, businesses will get a fair chance of lowering the supply chain disruptions, while identifying the complete value of their supply chain cycle. This adoption, however, can be difficult. This is where digital transformation companies like Appinventiv come into the picture. We don’t just help you with the software upgrade to become more responsive towards risk but also bring about a change in your business culture making them more conscious about management and mitigation of risks and market changes.

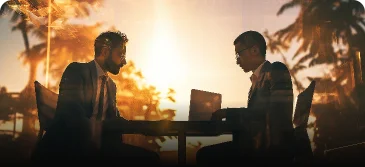
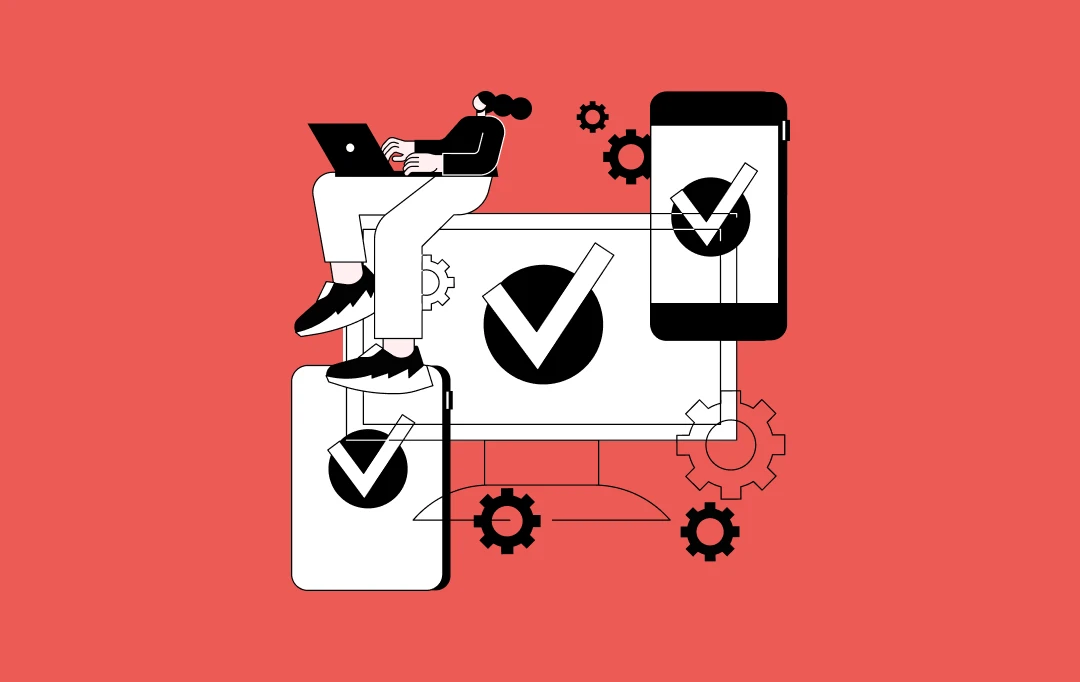
Enterprise Application Integration - How It Works and Why It Matters to Your Business
In the fast-paced corporate world, CEOs and CTOs are often tasked with managing multiple systems and departments, each playing a crucial role in the success of the company. But what happens when these systems don’t communicate effectively with one another? Imagine your sales team's inability to instantly share data with your inventory management or customer…
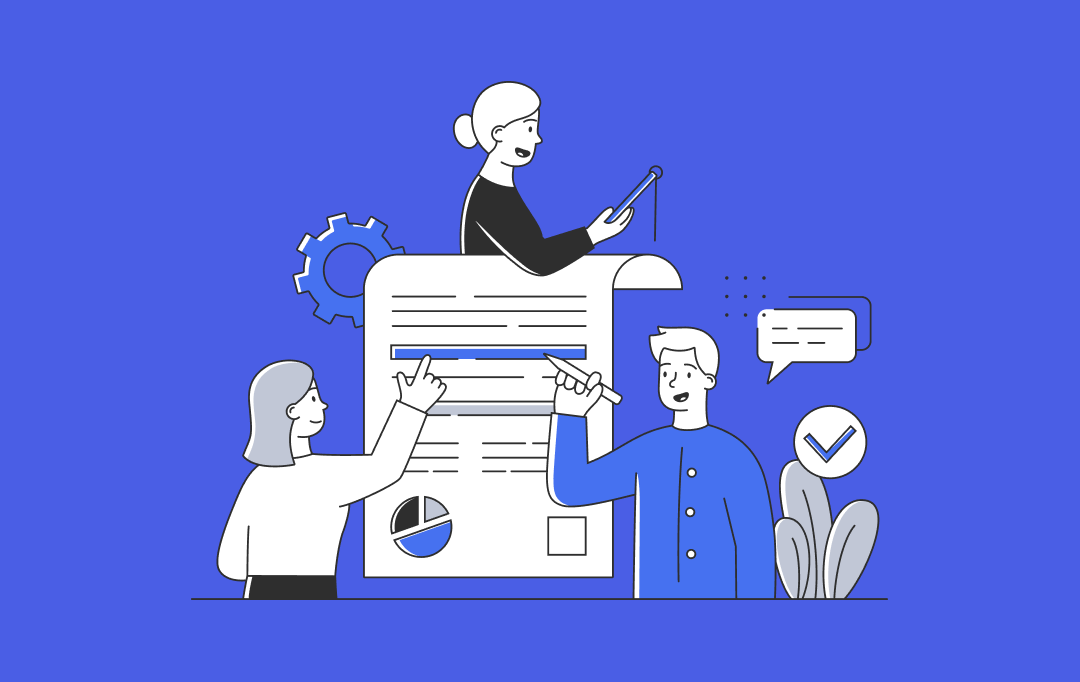
Mobile CRM - The Key to Driving Success in the Modern Business Landscape
In a world where business agility translates to success, embracing Mobile CRM can be a game-changer. It provides immediate access to customer data, significantly boosting your responsiveness and operational effectiveness in a competitive market landscape. These systems ensure that relevant customer information is just a tap away, enhancing decision-making, optimizing customer interactions, and significantly boosting…
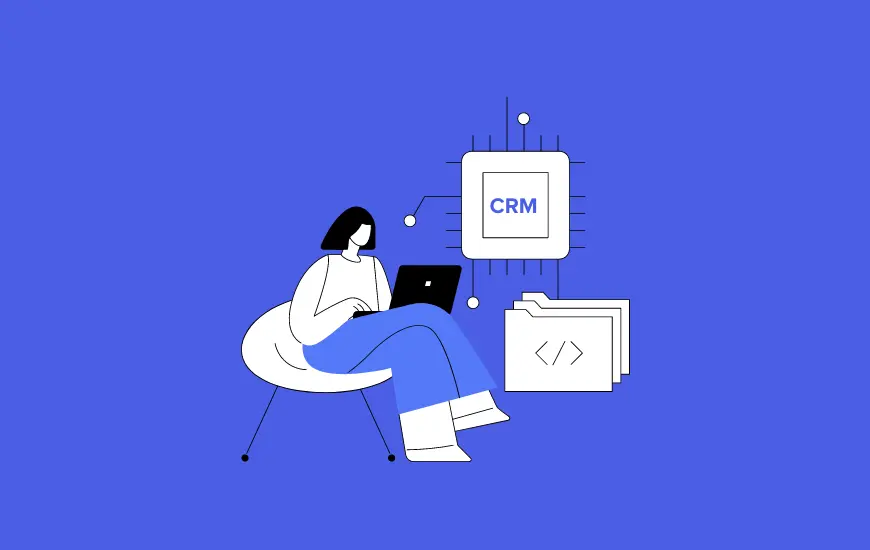