- Digital Twin Technology in Oil and Gas Industry - Key Benefits
- Safety and Emergency Preparedness
- Reduced Labor and Engineering Costs During Field Development
- Seamless Remote Monitoring and Control
- 10 Real-World Digital Twin Applications and Examples in the Oil and Gas Industry
- Asset Monitoring and Predictive Maintenance
- Process Optimization
- Design and Simulation
- Advanced Employee Training and Simulation
- Sustainability and Environmental Management
- Drilling and Completion Operations
- Well Optimization
- Value Chain Optimization
- Safety and Risk Management
- Pipeline Integrity Management
- Integration of Digital Twin with Key Trending Technologies
- IoT (Internet of Things)
- AI (Artificial Intelligence)
- Blockchain
- Addressing the Digital Twin Adoption Challenges in the Oil and Gas Industry
- Challenge 1: Data Inconsistencies
- Challenge 2: Cultural Resistance
- Challenge 3: Integration Challenges
- The Future of Digital Twin in Oil and Gas Industry
- Let Appinventiv Empower your Oil and Gas Endeavors!
- FAQs
Over the years, the oil and gas industry has found itself at the core of dynamic changes. While events like the COVID-19 pandemic and the Russia-Ukraine war have asserted atypical pressures, technological advancements such as Big Data, IoT, and AI have boosted productivity in the oil and gas sector.
As the sector is set to reach a market value of $7,652.82 billion by the end of 2024, the gradual adaptation of emerging technologies like digital twin in oil and gas will further catalyse the growth of said industry!
Digital twin technology can be perceived as a dynamic and visual representation of a physical asset or system created with real-time data. Be it healthcare, supply chain, or retail, the business applications of digital twin technology are numerous, and the oil and gas sector is no exception.
Digital twin technology in oil and gas has enabled massive transformation, granting the ease of remote monitoring and control to cost reduction and enhanced safety. Let’s delve deeper to decode the role of the digital twin in oil and gas along with its enormous implementations across the industry!
Digital Twin Technology in Oil and Gas Industry – Key Benefits
Initially leveraged by NASA to prepare space missions, digital twin technology has readily found profound applications in the oil and gas industry. In fact, by 2032, the global digital twin implementation in the oil and gas market is expected to attain a valuation of $912.1 million.
By integrating real-time operational data and advanced algorithms into a comprehensive digital model, digital twins allow you to predict future behavior accurately. However, this is just one small example of the many solutions it brings to the technology challenges in the oil and gas industry. Others include,
Safety and Emergency Preparedness
Safety is a major concern of the oil and gas industry, and digital twins help to enhance this component in multiple ways. For example, by integrating this advanced technology into the oil and gas industry, businesses can simulate various dangerous scenarios in a risk-free environment, thereby facilitating employee training. The team members can learn new skills and know how to respond to safety emergencies without having to risk their lives repetitively during such training sessions.
Reduced Labor and Engineering Costs During Field Development
One of the major benefits of digital twin technology in the oil and gas industry is that it saves significant time, which otherwise would have been spent on field development. By integrating it with machine learning and high-level data analytics, you can create virtual models of oil and gas reservoirs.
Furthermore, with the help of real-time sensor data, the digital twin can accurately estimate the yield potential of the reservoir and can also provide aid in optimizing drilling.
Seamless Remote Monitoring and Control
A constant vigilance is a must for all businesses operating in the oil and gas industry. However, the same can often get difficult, especially in hazardous and challenging locations. Thanks to the prowess of the digital twin, you can now access real-time visibility into equipment and processes at any site, thereby allowing for remote monitoring and control. It serves as the ultimate supervisor, facilitating collaborative teamwork and effective decision-making.
Also read: Digital Twins in Construction – Benefits, Use Cases, Implementation, and More
10 Real-World Digital Twin Applications and Examples in the Oil and Gas Industry
Considering the diverse set of advantages it attracts, the trend of adopting digital twins in oil and gas is expanding at a rapid pace across the globe. Besides saving millions of dollars and productivity hours for industries worldwide, digital twin technology lies at the heart of key sustainability efforts made by around 57% of organizations.
To further decode its efficacy and myriad implementations, let’s decode a few oil and gas digital twin technology use cases.
Asset Monitoring and Predictive Maintenance
Let’s be honest: Sudden equipment failures and outages can be very frustrating, not to mention the amount of work and revenue wasted. Thanks to the amazing capabilities of oil and gas digital twins, you can now create virtual copies of physical assets such as pumps, compressors, and turbines. This will enable you to monitor equipment health, detect early signs of failure, and even identify potential opportunities for improvement.
Example:
BP, a leading multinational oil and gas company, has successfully cracked this code and utilized digital twin technology to monitor its offshore platform’s equipment. This has ultimately resulted in timely prediction, reduced maintenance costs, and increased efficiency of operations.
Process Optimization
Another notable example of an advanced digital twin application is its ability to offer real-time performance monitoring and optimization. By integrating AI with digital twin technology, you can access more predictive analytics and machine learning capabilities, ultimately leading to increased efficiency and innovation in oil and gas operations.
Example:
ExxonMobil, a major player in the industry, has observed tremendous growth by utilizing digital twin technology to generate replicas of its full liquefied natural gas (LNG) operations. This has allowed the organization to perform simulations, identify bottlenecks, and optimize all processes. As a result, the organization boosted efficiency and improved its decision-making process.
Design and Simulation
With the help of digital twins in the oil and gas industry, multiple team members can collaborate in the virtual mode, regardless of their physical location.
The ultimate result? Better design choices, faster project completion, and overall reduced costs.
This has been a tremendous advantage, especially for engineers, as they can now test and refine processes in a virtual environment before going forward with the implementation in the real world.
Example:
By incorporating this technology into the preproduction phase of its deepwater oil and gas fields, Shell has been able to test different configurations and determine the safety and operational efficiency of the infrastructures before actual deployment.
Advanced Employee Training and Simulation
As already mentioned earlier, digital twins in the oil and gas industry facilitates advanced training and simulation opportunities for personnel. It allows you to replicate real-world scenarios in an environment devoid of any risk, thereby empowering employees to hone their on-site operational skills and gain valuable experience without putting their lives at risk from time to time.
Example:
Equinor has been successful in creating a virtual replica of an oil and gas production plant, which serves as a key risk-free environment wherein employees can directly interact with the complexities of operational processes and develop essential skills.
Sustainability and Environmental Management
The increasing importance of digital twin technology in the oil and gas industry can be viewed in its ability to promote sustainability and environmental management. Digital twins allow enterprises to simulate operational impacts and ecological conditions, hence mitigating the environmental footprints.
From reducing emissions and managing waste to complying with environmental regulations, it facilitates the development of effective strategies that are in sync with global sustainability goals.
Example:
Total Energies is a fantastic example of a reputed firm in this industry that uses digital twins to monitor and control the environmental impact of its activities. By modelling emissions and energy use, the company was able to identify major areas for improvement and assure compliance with environmental requirements.
Drilling and Completion Operations
Oil and gas digital twins enable enterprises to simulate different drilling scenarios while also providing insights into accuracy and the best ways to streamline operations. It carries dual advantages for businesses. Firstly, by modeling your drilling options, you avoid the risk of unexpected issues. Secondly, you can try out multiple variations without spending extra resources or workforce in such trials.
Example:
Eni recently completed a virtual model of its Scarabeo 8 ultra-deepwater semi-submersible drilling rig. This enabled the organization to reach its ultimate goal of boosting rig safety, performance, and well planning.
Well Optimization
The use of digital twins to create virtual models of wells has proved to be an effective way to increase overall efficiency. By collecting real-time data from sensors, simulating the behavior of the wells, and assessing the impact of various factors such as pressure, flow rate, or temperature, enterprises can avoid potential issues when the well is functioning without the worker’s direct involvement.
Example:
Rosneft created a digital model of Sibneftegaz fields, simplifying the entire monitoring of well operation. The dynamics of changes in well operation parameters can be visualized on graphs, and with the help of this technology, the enterprise was also able to predict the natural gas production levels for short-medium terms (month-year).
Value Chain Optimization
In addition to enhanced operational efficiency, the use of this advanced technology in the oil and gas industry can also facilitate supply chain optimization. Maintenance teams can simulate the entire supply chain, gaining full visibility into operations and logistics and detecting any potential bottlenecks.
Example:
ADNOC, one of the early adopters of digital twins in the oil and gas industry, was able to simulate its entire value chain, encompassing wells to customer delivery. It could test different scenarios that further improve the decision-making process.
Safety and Risk Management
Digital twins can simulate a wide array of scenarios to help operators optimize operational procedures and mitigate potential risks. Take this small situation as an example. A digital twin of an oil pipeline system can detect any potential leaks or ruptures, thereby enabling personnel to take the necessary course of action before a dangerous malfunction occurs.
Example:
Petrobas utilizes this technology to enhance safety in all its operations. The digital models can simulate potential hazard scenarios and provide early warnings, thereby improving overall safety management.
Pipeline Integrity Management
Integrated digital twin, when combined with pipeline management tools and predictive analytics, carries numerous benefits for an organisation. It not only helps to improve pipeline performance and integrity but also allows for better collaboration and reduced pipeline downtime, by quickly responding to early signs of asset failure.
Example:
Enbridge has successfully reaped the benefits of this technology by creating a digital twin of its vast and extensive pipeline network. This has not only enabled the company to conduct virtual inspections and simulations but also fostered a proactive approach to any risks detected through predictive analytics, guaranteeing a safe and efficient transport of oil and gas overall.
These are some of the core digital twin use cases in the oil and gas industry. However, digital twin implementations are not limited till here. Perceiving its limitless advantages, digital twin’s applications are expanding over time!
Integration of Digital Twin with Key Trending Technologies
A recent report by McKinsey stated that almost 75% of companies worldwide have already adopted digital twin technologies. Needless to say, the potential of this technology to revolutionize every industry, including the oil and gas domain, is fueling rapidly.
One key trend that can be viewed in this aspect is the integration of digital twins with other advanced technologies, such as AI, IoT, and blockchain.
IoT (Internet of Things)
The synergy between digital twins and IoT is powerful, to say the least. Consider this, digital twins essentially require a constant stream of data to effectively mirror their physical counterparts. IoT devices in the oil and gas sector, equipped with sensors, collect real-time data on environmental conditions, user interactions, and the performance of specific objects.
AI (Artificial Intelligence)
AI in oil and gas can enhance predictive analytics and maintenance by analyzing large amounts of patterns and data from digital twins. It can accurately forecast when a machine might break down or when a system might go offline. It’s like knowing in advance that your car’s tire might go flat next week so that you can take the necessary steps beforehand.
From a business point of view, AI has proved to be hugely advantageous in terms of sky-high efficiency and reduced unexpected costs.
Blockchain
Data privacy and security are key concerns of every industry, not just the oil and gas domain. In fact, according to a recent report by IBM, the global average cost of a data breach in 2024 was estimated to be $4.88 million. To prevent such occurrences and, most importantly, cut down on such expensive breach costs, blockchain can be used to validate and secure data transactions between the digital twin and other systems.
Addressing the Digital Twin Adoption Challenges in the Oil and Gas Industry
Despite the advantages of the oil and gas digital twins listed above, businesses commonly face quite a few challenges during the adoption of this technology. Let’s explore some of the core challenges to decode how they’re being addressed by industry leaders!
Challenge 1: Data Inconsistencies
Most companies with a digital twin refinery struggle with inconsistent data collection, where sensors might provide incomplete or inaccurate information. This can, in turn, result in less reliable digital twin outputs.
Solution: To prevent the occurrence of such instances, it is paramount for every business to invest in robust data governance, and high-quality sensory technology. Additionally, refineries need to standardize their data collection practices so that they can ensure that only high-quality and reliable data are fed to the digital twin, ultimately resulting in accurate simulations and analytics.
Challenge 2: Cultural Resistance
Technological transformations can result in a significant cultural shift within an organization. This is especially true because most team members or employees who are already accustomed to the traditional operational methods may be hesitant to make new changes. This can not only result in a delay in the implementation process but also disrupt the entire efficiency of the workforce.
Solution: The key is to provide ongoing training and education, with clear communication that states the importance of the adoption of this technology alongside its benefits. By engaging employees in the transformation process, you can help mitigate the risk of resistance and foster a proactive approach to highlighting the importance of new technology in the oil and gas industry.
Challenge 3: Integration Challenges
Integrating digital twins with the already existing IT infrastructure can pose technical challenges for many. In fact, many businesses continuously suffer from failed projects due to the lack of a cohesive strategy that is in sync with the operational workflow of refineries.
Solution: To avoid such drastic consequences, it is very important for companies to devise a comprehensive integration plan. This includes involving stakeholders from multiple departments to guarantee that the solutions are scalable and, most importantly, meet the operational needs without any hindrance to existing workflows.
The Future of Digital Twin in Oil and Gas Industry
According to McKinsey– “The journey towards the enterprise metaverse, while still aspirational, has already begun with the development of the engines that power it: digital twins.”
Needless to say, with the emergence of this technology, the lines between physical and digital environments have become increasingly blurred. As more and more enterprises leverage the advantages of digital twins in oil and gas to improve their operational efficiency and develop better safety procedures, the future of this sector looks promising.
However, to fully harness the potential of digital twin in oil and gas, companies operating in this domain need to overcome some of its barriers. These include investing in proper digital skill development for their workforce, fostering a culture of innovation and agility, and effectively navigating the complexities surrounding data ownership and privacy.
Let Appinventiv Empower your Oil and Gas Endeavors!
For oil and gas businesses that wish to thrive in this digital world, investing in digital technology is no longer an option; it is a necessity. From operational efficiency, risk management, to strategic planning and sustainability, the list of benefits that this technology brings to the table is endless. The key is to remain agile by embracing these advancements and staying competitive and relevant in a rapidly evolving landscape.
Appinventiv, with its expertise in oil and gas software development services, helps enterprises integrate top-notch IT solutions that can effectively automate and manage their business operations.
Be it refinery scheduling or field service management, our team of professionals is dedicated to providing personalized service that caters to the evolving needs of the dynamic energy industry.
Consult our team of experts and achieve excellence by developing industry-focused oil and gas software solutions!
FAQs
Q. What is digital twin in oil and gas?
A. In simpler terms, digital twin oil and gas replicate the attributes and features of a physical asset by using real-time data. With the help of this, enterprises can enhance their safety and operational efficiency, unlock predictive maintenance, and access remote monitoring, among other benefits.
Q. How does digital twin technology help in achieving maximum efficiency and safety in oil and gas?
A. Predictive maintenance is one of the key capabilities of digital twins in the oil and gas industry. By accurately predicting equipment failures and enabling preemptive maintenance, businesses can reduce downtime, and avoid potential financial losses and safety challenges.
Q. How much does it cost to implement digital twin technology in the oil and gas industry?
A. There is usually no single cost for digital twin oil and gas implementation. It can vary from $50,000 – $400,000+, depending on multiple factors such as deployment, integration, maintenance, size of the company, and design cost, among others.
Q. What is the environmental impact of leveraging digital twin technology in the oil and gas industry?
A. One of the main challenges faced by the oil and gas industry is the reduction of its environmental impact. The integration of digital twin technology in the oil and gas industry has proved to be invaluable in this aspect. By simulating operations and their environmental impact, enterprises are now able to devise strategies to reduce emissions, manage waste, and guarantee adherence to environmental regulations.
Q. Are there any potential disadvantages of digital twins in oil and gas?
A. Digitalization in the oil and gas industry with digital twin technology has a few cons as well. These include substantially high implementation costs, cybersecurity concerns, data management challenges, and integration-related complexities. However, partnering with expert-led enterprises, such as Appinventiv, can help effectively tackle such issues. Connect with us!
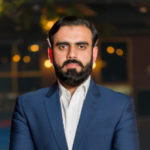
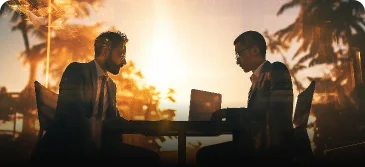
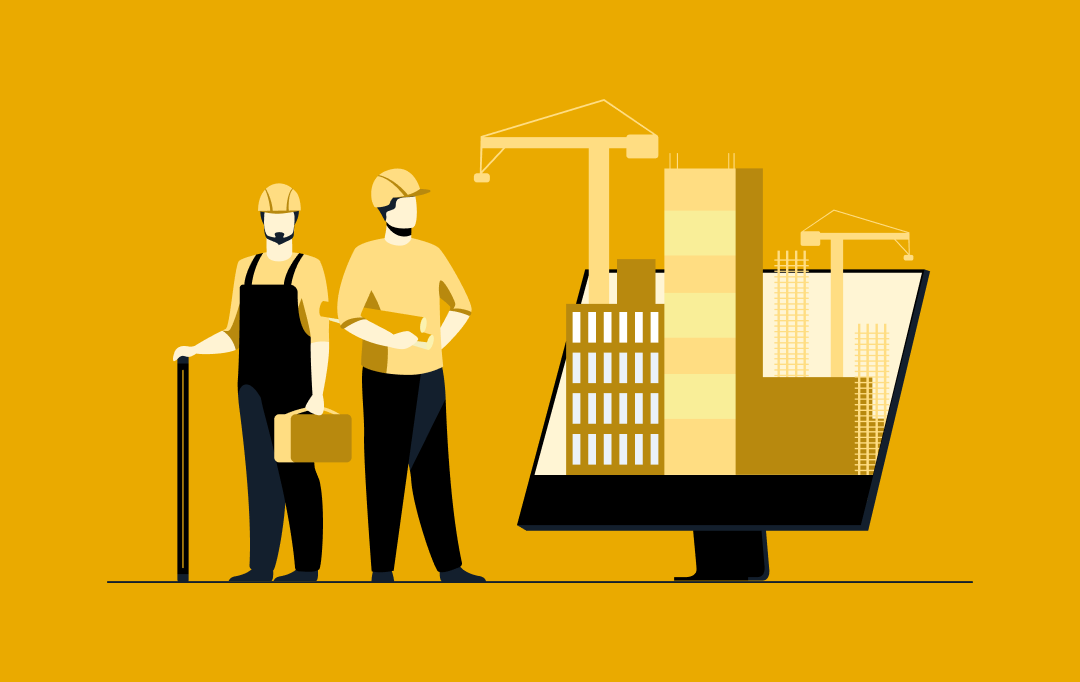
How Digital Transformation is Shaping the Next Era of Construction
The construction industry, traditionally slow to adopt new technology, is now actively embracing digital transformation, marking a significant shift towards modernization and increased productivity. This change is all about adopting new solutions that enhance efficiency, safety, and project management, offering significant benefits to businesses. While the complexity of construction projects and coordination among multiple parties…
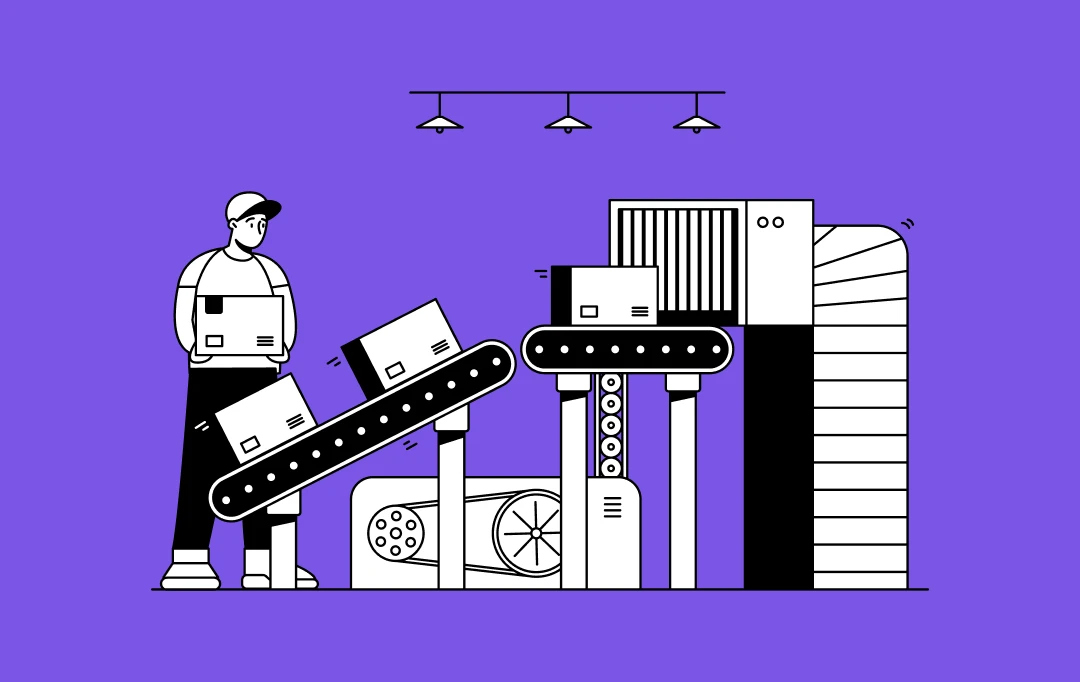
How Digital Twins Act as Key to Smarter and More Agile Manufacturing Processes - 10 Use Cases and Examples
Tapping into the potential of digital twins in manufacturing, businesses today are creating a transformative virtual, real-time counterpart of physical systems, making it easier to monitor, assess, and optimize their manufacturing operations. McKinsey highlights the value of this approach, pointing out how “a company with a robust digital-twin platform can conduct comprehensive full-product simulations in…
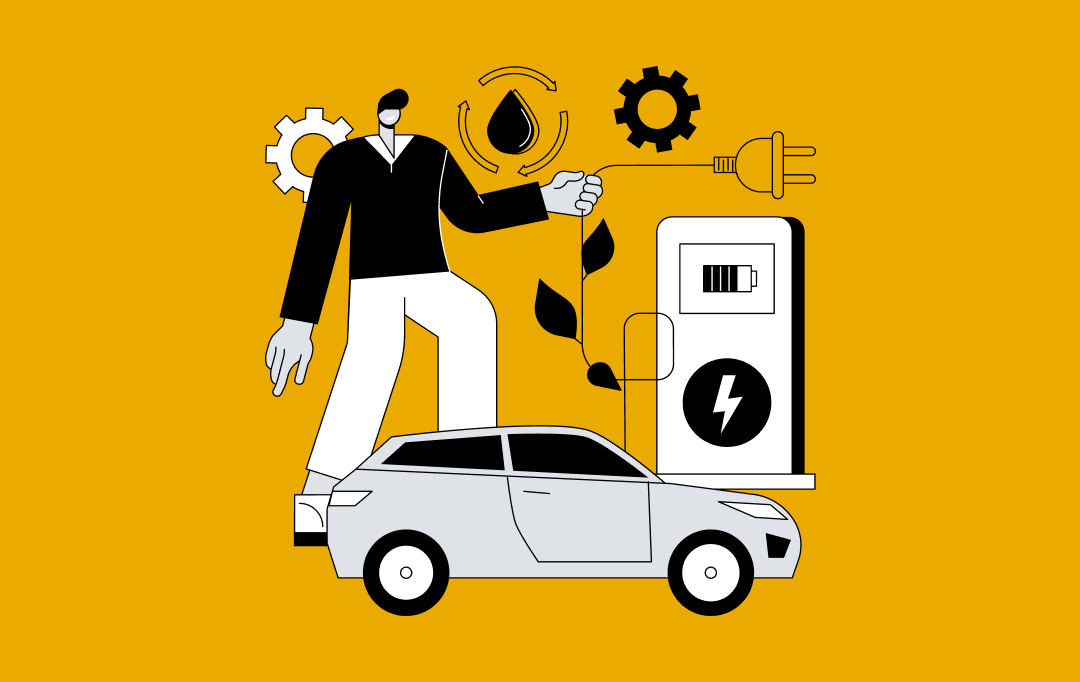