- Why Digital Twins? Understanding the Benefits of Digital Twin Manufacturing
- Remote monitoring
- Better collaboration
- Cost efficiency
- Superior predictive maintenance
- Enhancing product quality
- Improved analytics
- Implementation of Digital Twins in Manufacturing: Top 10 Use Cases
- Use Case 2: Enable Predictive Maintenance
- Use Case 3: Optimize Product Performance
- Use Case 4: Reduce Time to Market Product
- Use Case 5: Personalized User Experience
- Use Case 6: Risk Mitigation
- Use Case 7: Testing New Products
- Use Case 8: Staff Training
- Use Case 9: Streamline Operations
- Use Case 10: Safe Manufacturing
- Additional Compatible Technologies with Digital Twins
- Challenges of Digital Twin in Manufacturing
- Integration Complexity
- High Initial Costs
- Data Management
- Scalability Issues
- Security Concerns
- Skill Shortage
- Future Trends of Digital Twins in Manufacturing
- Digital twins as cloud-based solutions
- Fusion with XR (extended reality)
- Emphasis on the environmental impact
- Integration of Edge Computing
- Harness the Potential of Virtual Twins with Appinventiv’s Digital Twin Technology Services
- FAQs
Tapping into the potential of digital twins in manufacturing, businesses today are creating a transformative virtual, real-time counterpart of physical systems, making it easier to monitor, assess, and optimize their manufacturing operations.
McKinsey highlights the value of this approach, pointing out how “a company with a robust digital-twin platform can conduct comprehensive full-product simulations in a virtual environment before any proposed design is signed off on by the customer.” This further asserts its unmasked potential that domains like manufacturing today are fully utilizing!
The role of digital twins in manufacturing today is helping businesses across diverse domains to take an innovative approach to product development. This approach stems from the ability to virtually replicate physical systems, enabling organizations to increase productivity, encourage better decision-making, and significantly cut down costs.
According to a report by Grand View Research, the digital twin market size was valued at $16.75 billion in 2023 and is expected to reach $155.84 billion by 2030, witnessing a CAGR of 35.7% from 2024 to 2030. Given the provided statistics, we can confidently assume that the impact of digital twins in the manufacturing industry will only grow with time.
Let us delve into the significance of this technology, decoding the key benefits of the technology by going through its various use cases!
Why Digital Twins? Understanding the Benefits of Digital Twin Manufacturing
A study shows that 29% of global companies have already made the implementation of digital twins in manufacturing a reality. Agile manufacturing relies heavily on digital twins as they offer a virtual version of real assets and systems that enable real-time analysis, monitoring, and optimization. As a result, digital twin technology in manufacturing lets companies react swiftly to shifts in demand, market dynamics, and production difficulties at a time when agility is critical.
Digital twins reduce downtime and increase operational efficiency by integrating real-time data to predict maintenance needs and optimize production schedules. They make product testing possible, enabling manufacturers to make adjustments or take novel approaches without interfering with ongoing production.
From optimizing product performance to staff training to streamlining operations, digital twin technology’s growing use across companies for agile manufacturing is not a surprise at all!
[Also Read: Digital Transformation: What Manufacturers Need to Know About the Imperative Change]
Before diving into the implementation, let’s look at the various benefits of digital twins in manufacturing in detail below.
Remote monitoring
It is frequently very difficult, if not impossible, to obtain a real-time detailed overview of a large-scale physical system. Nonetheless, users can view and monitor the system performance remotely due to the digital twins’ accessibility from any location.
Better collaboration
Thanks to process automation and round-the-clock access to system information, technicians can concentrate more on teamwork and operational efficiency. Digital twin manufacturing makes this possible, enabling smooth collaboration among team members.
Cost efficiency
Before making changes in the actual world, the business can test various materials or production techniques in a virtual setting by using a digital twin in manufacturing. This could lead to a cheaper, more effective production process, fewer prototypes, and less material waste.
Superior predictive maintenance
A digital twin system’s IoT sensors provide a lot of data in real time, which companies may use to analyze and proactively spot system issues. This functionality helps them lower maintenance costs, increase production line efficiency, and plan predictive maintenance more precisely.
Enhancing product quality
By offering a virtual model that enables real-time manufacturing process monitoring, modeling, and optimization, digital twins improve the quality of products. They make it possible for predictive maintenance, continuous improvement, and early defect identification. This increases manufacturing precision and eventually produces better products with fewer mistakes.
Improved analytics
A substantial amount of data is available to power digital twins, sourced from various channels, including sensors, floor machines, production line data, design data, inspection data, and user and historical data. By utilizing all this data, virtual twins in manufacturing can enhance analysis and decision-making in operations.
Implementation of Digital Twins in Manufacturing: Top 10 Use Cases
To help you understand the impact of digital twins in the manufacturing industry, you should first have some information about the digital twins applications in manufacturing. Let’s take a glance at some significant use cases of digital twins in manufacturing.
Use Case 1: Boost Production Efficiency
With the use of digital twins, operators can keep an eye on systems and processes all the time, determining which ones work best.
A digital twin in the manufacturing industry will show areas that can be improved right away if the production flow isn’t working at its best. Smart manufacturing companies can reduce energy and material usage and achieve sustainability goals by using digital twins to increase production efficiency.
For instance, Shell optimizes production and boosts safety on its offshore platforms by utilizing digital twins. The implementation of digital twins in manufacturing helps it to view and simulate numerous scenarios as it gathers real-time data from multiple sensors on the platform. This further aids in optimizing platform operations and spotting errors before they become serious.
Use Case 2: Enable Predictive Maintenance
Unplanned downtime can cost tens of thousands of dollars per hour in smart manufacturing! Thanks to digital twins, operators can foresee problems based on various environmental forces and scenarios. Manufacturers can forecast when problems will arise and address maintenance difficulties before they take down production entirely by manufacturing digital twin software to examine the internal operation.
The experts at Phoenix Contact combine simulation findings and real-time sensor data with algorithms to forecast problems ahead of time.
Responding to the demand of customers for space-saving technology, the company developed smaller elementary relays. To understand and manage the electromechanical, structural, and thermal interactions of these relays, Phoenix Contact employed digital twin technology in the manufacturing process.
Use Case 3: Optimize Product Performance
Smart manufacturers can forecast the final product’s quality by using a digital twin, which empowers them to make better-educated choices regarding aspects like process and material improvements. Digital twins are used in industrial manufacturing to maintain consistency throughout large-scale production, ensuring that the final product always meets the criteria.
Use Case 4: Reduce Time to Market Product
Smart manufacturers can make quick judgments about production by using digital twins, which create a virtual counterpart of the actual asset that is connected to it. The elimination of delays related to physical items, such as labor, materials, and hardware, allows operators to expedite all stages of the production process, covering design, development, testing, and maintenance.
Use Case 5: Personalized User Experience
Personalization is essential in today’s consumer-driven world. Fortunately, by digital twins’ courtesy, manufacturing businesses can provide tailored recommendations today based on a customer’s past purchases and preferences. These virtual copies guarantee a smooth user experience by helping owners with troubleshooting and even scheduling maintenance after the sale.
Use Case 6: Risk Mitigation
One significant role of digital twins in manufacturing is risk mitigation. Manufacturers can spot hard-to-track problems and design faults early in the process by employing digital twins in their design planning process. This proactive strategy lowers the possibility of expensive mistakes and rework in later stages of product development by enabling quick modifications.
Use Case 7: Testing New Products
Frontline employees no longer have to put up with the laborious trial-and-error procedure to test new products. With the introduction of digital twins, manufacturing companies can now test updated setups with a far lower chance of expensive calculation errors. This technology is now on its way to surpass physical testing, granting better speed, ease of use, and efficiency by modeling numerous scenarios before their physical structures.
For example, London’s Crossrail is a significant infrastructure project in which the engineers employed digital twins to see what the final product will look like. They were also able to monitor the project’s development and identify any possible problems. To improve throughput, they optimized and simulated the construction process using digital twins, cutting down substantial costs on potential wastage of resources while fueling productivity.
Use Case 8: Staff Training
Digital twin in the manufacturing industry can be used to train staff members and simulate real-world situations, giving them experience and knowledge without running the danger of physical harm or damage. Workers can learn how to operate machinery, solve issues, and increase productivity by building a digital twin of a production line. This can raise employee productivity, lower training expenses, and enhance the overall workforce safety.
Use Case 9: Streamline Operations
A manufacturing company should be aware of the use of digital twins in streamlining operations. Digital twins can simulate various operational scenarios, allowing users to easily understand the impact of different parameters. A detailed insight into such aspects can be utilized to improve operations, raise productivity, and fuel efficiency across various manufacturing organs.
Use Case 10: Safe Manufacturing
Recognizing possible risks in manufacturing is not always a straightforward process. However, digital twins can be useful for assessing any safety risks in advance and taking appropriate action by modeling various situations.
If you’re introducing a new machine, you can create a digital twin to simulate its operation before the physical equipment is in use. This allows you to observe its performance and identify potential safety issues, prioritizing safety in addition to meeting production needs.
Additional Compatible Technologies with Digital Twins
Now that you know about the various use cases of digital twins in manufacturing, you must learn about some complementary technologies that are used with digital twins.
In the manufacturing industry, digital twins collaborate with a range of state-of-the-art technologies to optimize their performance. By combining such technologies, digital twins become more reliable and adaptable in the manufacturing process.
Companies need to make sure their data historians and software platforms allow third-party integration of these technologies to fully realize the promise of producing digital twins. This interoperability improves the accuracy and functionality of the manufacturing digital twin software by facilitating smooth data interchange and the integration of diverse technologies.
Some of these compatible technologies are given below:
VR (Virtual Reality): Through more immersive and natural interactions with the digital twin made possible by VR technology, operators and engineers may better comprehend and analyze production processes.
ML (Machine Learning) and AI (Artificial Intelligence): Large-scale data created by digital twins is analyzed by machine learning and artificial intelligence algorithms. These provide predictive insights and automate the decision-making process to boost manufacturing methods.
Also Read: How AI Is Proving to be a Game-Changer in Manufacturing – Use Cases
IoT (Internet of Things): Digital twins are fueled by real-time data from IoT devices, which makes precise simulations and analysis possible. The digital twin in the manufacturing industry is created by mirroring the actual environment’s data, which is gathered and monitored by sensors and linked IoT devices.
Challenges of Digital Twin in Manufacturing
As digital twin technology has the power to reshape the landscape of manufacturing, it also brings with it a set of challenges that businesses must navigate. Here’s how companies can tackle the challenges of digital twin in manufacturing effectively:
Integration Complexity
Integrating digital twins with existing systems can be a complex process that seems to be challenging for certain businesses. To resolve this, businesses should employ a phased integration approach that starts with critical areas to minimize disruption and paves the way for gradual adaptation.
High Initial Costs
The upfront investment for implementing digital twins can be significant for businesses. In order to keep the initial costs in hand, they should focus on pilot projects to demonstrate ROI and expand as cost savings and efficiencies become apparent.
Data Management
Managing the vast amounts of data generated by digital twins requires robust systems. Businesses can, in turn, implement advanced data analytics platforms and employ data management practices that enhance data security and integrity.
Scalability Issues
Scaling digital twin solutions across different departments can be a difficult process. Businesses should design digital twins with scalability in mind from the start, using modular frameworks that can be expanded as needed.
Security Concerns
Protecting the data and processes associated with digital twins is critical. In order to resolve this, companies can utilize cybersecurity measures like encryption and access controls, and regularly update security protocols to guard against threats.
Skill Shortage
The lack of professionals trained in digital twin technologies presents a big challenge for the businesses. To handle this, they can partner with a specialized development firm that can provide access to a pool of experts who are already skilled in digital twin technology, eliminating the need for extensive internal training and accelerating implementation.
Future Trends of Digital Twins in Manufacturing
We are at the cusp of a new era in technology, and as we look to the future of virtual twins in manufacturing, exciting things are going to happen that will change industries. Let’s check out in detail what the future trends of digital twins in manufacturing looks like for businesses:
Digital twins as cloud-based solutions
As cloud-based solutions gain popularity, digital twin technology is about to become more accessible. Accessibility and affordability for companies of all sizes are promised by this change. Cloud platforms will free digital twins from the limitations of complex IT systems by ensuring safe data storage, processing power, and global accessibility.
Fusion with XR (extended reality)
This combination of extended reality with digital twins will create immersive experiences that transform decision-making, cooperation, and visualization. Engineers and technicians will use digital twin data to overlay physical assets with real-time guidance. The borders between the digital and physical worlds will vanish with XR integration, opening up new possibilities for remote collaboration, troubleshooting, and training.
Emphasis on the environmental impact
Digital twins of the future will put sustainability at the forefront. Companies will use the technology to maximize resource efficiency, lower carbon emissions, and optimize energy use. Digital twins will become essential for achieving environmental objectives, from creating eco-friendly product designs to developing sustainable urban planning strategies.
Also Read: Green AI: How Artificial Intelligence Can Solve Sustainability Challenges
Integration of Edge Computing
Edge computing capabilities will be integrated into digital twins in the future, allowing for real-time analytics and decision-making at the edge of networks. Digital twins can process data closer to the source, allowing them to react quickly to changing conditions and offer instant insights. Edge computing will improve data security, lower latency, and allow for more effective use of network bandwidth.
Harness the Potential of Virtual Twins with Appinventiv’s Digital Twin Technology Services
As we conclude our discussion on digital twins and the various use cases of digital twins in manufacturing, we hope our detailed analysis will encourage you to explore more about this transformative technology.
Curious how to initiate your journey with digital twins? Partnering with Appinventiv for digital twin technology offers you access to a team of experts who specialize in the latest advancements and have a proven track record of delivering successful projects.
As a dedicated manufacturing IT services provider, our skilled professionals excel in integrating digital twin technology to streamline manufacturing processes, enhance product performance, and reduce operational costs. Our approach combines cutting-edge solutions with tailored strategies to meet specific business needs, ensuring that each solution not only aligns with but also accelerates your operational goals.
With our expertise, you can explore new possibilities in digital twin technology, opening doors to improved efficiency, enhanced product quality, and reduced time to market. Get in touch with us if you are ready to explore the untapped potential of digital twins for your manufacturing business!
FAQs
Q: What is digital twin in manufacturing?
A: Digital twin in manufacturing is an electronic duplicate of a system or process used in manufacturing. This digital replica might be anything from a graphic representing equipment data to a full-fledged manufacturing line simulation model. Manufacturers can monitor, evaluate, or optimize the process using this twin instead of spending money on costly field tests.
Q: Why are the benefits of digital twins in manufacturing?
A: By leveraging digital twin technology in manufacturing, businesses can shift their focus from manual data manipulation to strategic problem-solving. This technology provides a comprehensive view of performance metrics, enabling proactive maintenance, productivity improvements, and better decision-making. Furthermore, digital twins also allow manufacturers to predict failures, streamline operations, and make informed decisions efficiently, ultimately driving business advancement.
Q: What is an example of a digital twin in manufacturing?
A: An example of a digital twins in manufacturing is its ability to predict the quality of the final products. This technology helps businesses make informed decisions about material and process enhancements. By ensuring consistency across large-scale production, digital twins confirm that every product meets the required standards, effectively maintaining high-quality outputs in industrial settings.
Q: How is IoT used in digital twin manufacturing?
A: By obtaining real-time data using sensors on IoT devices, this technology interacts with digital twins, powering it to make data-based analyses and offer relevant insights. For instance, digital twins of a manufacturing unit are connected to manufacturing equipment with IoT sensors. This helps keep track of all the changes and the overall health of the manufacturing equipment.
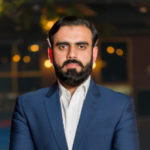
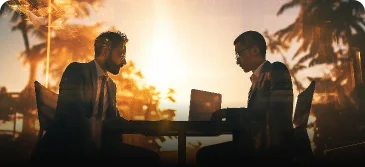
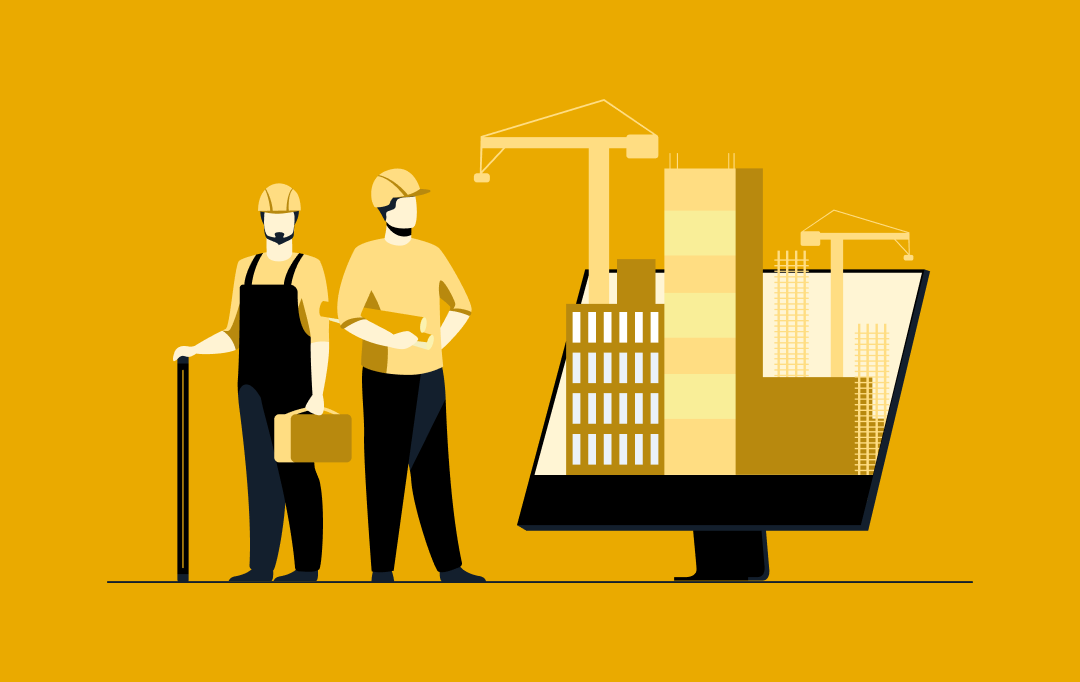
How Digital Transformation is Shaping the Next Era of Construction
The construction industry, traditionally slow to adopt new technology, is now actively embracing digital transformation, marking a significant shift towards modernization and increased productivity. This change is all about adopting new solutions that enhance efficiency, safety, and project management, offering significant benefits to businesses. While the complexity of construction projects and coordination among multiple parties…
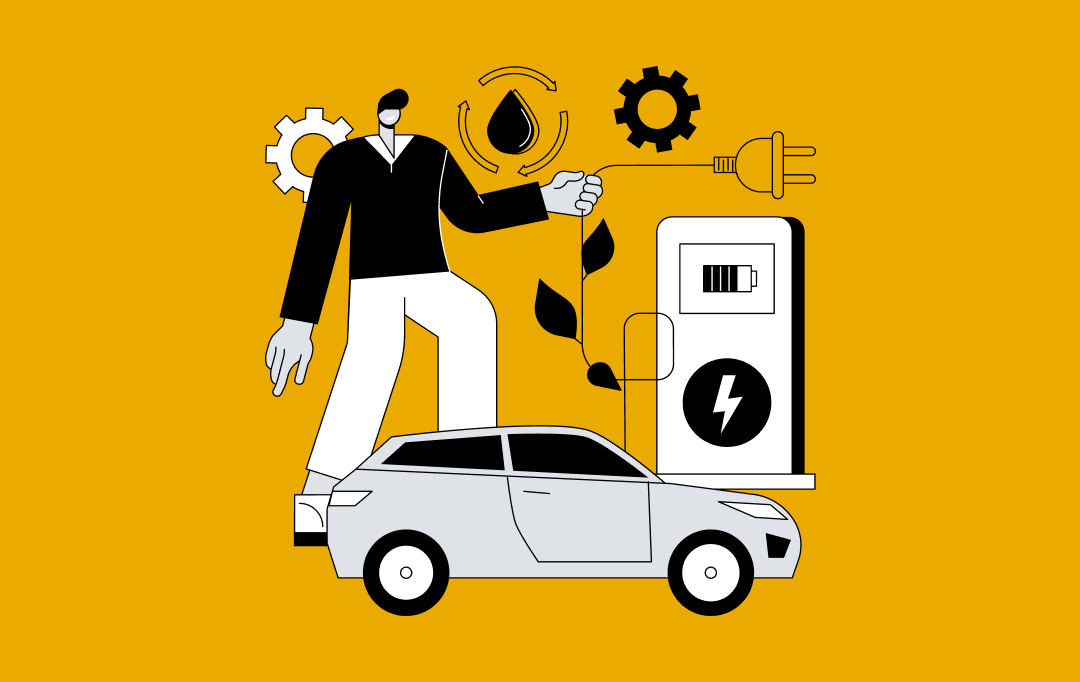
How Digital Twins Are Driving Innovation in the Energy Sector - Benefits, Uses Cases and Real Examples
The energy sector, with its expansive growth and evolving demands, encounters a range of challenges, from aging infrastructure to operational inefficiencies and strict environmental regulations. As companies navigate these complexities, the need for innovative solutions becomes increasingly apparent. In this context, the digital twin technology emerges as a game-changing advancement, providing a sophisticated method for…
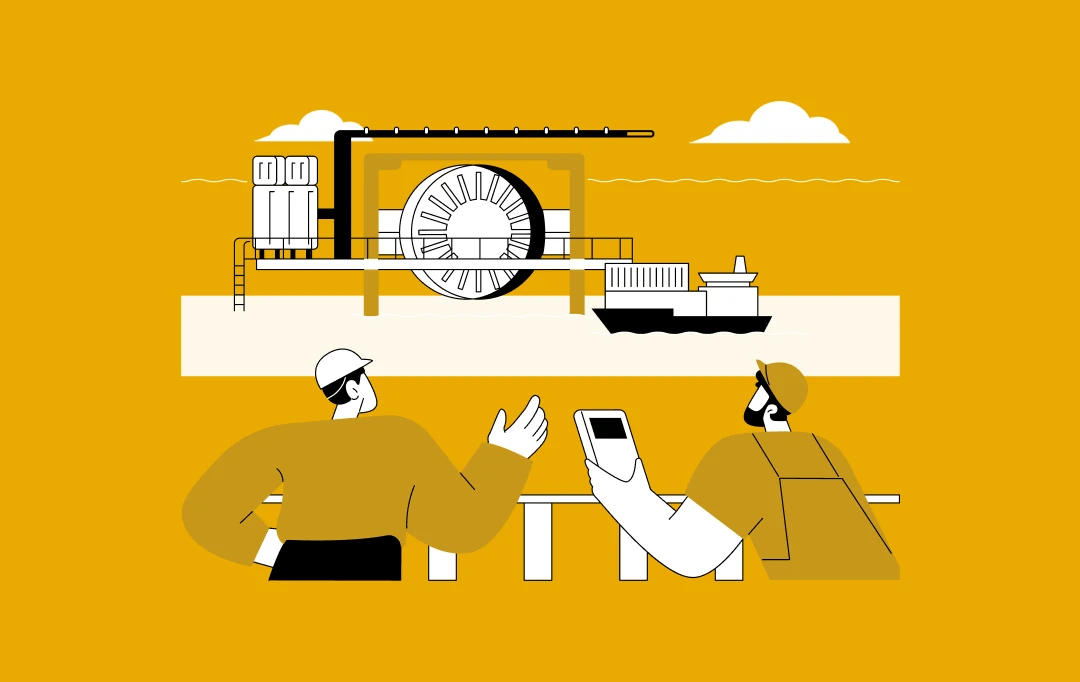