- Introduction
- Generative AI in Manufacturing
- Generative AI for Manufacturing: 10 Game-Changing Use Cases
- Supercharging Product Design
- Predictive Maintenance on Steroids
- Demand Forecasting Done Right
- Custom Manufacturing
- Effective Supply Chain Management
- Quality Control On Track
- Smart Workforce Management
- R&D Innovation Going Fast
- Automate Documentation and Compliance
- Energy Consumption
- Some Real-Life Examples of Generative AI in Manufacturing Industry
- Predictive Maintenance
- Quality Control
- Production Optimization
- Key Benefits of Leveraging Generative AI for Manufacturing
- Streamlined Designing
- Process Optimization
- Predictive Maintenance
- Data-Driven Decision Making
- Sustainability Improvements
- How to Implement Generative AI in Manufacturing Workflow?
- Gather all the data
- Cleanse Your Data
- Train Your AI Model
- Plug It Into Your Systems
- Keep Learning, Keep Evolving
- What are the Challenges with the Adoption of Generative AI in Manufacturing Industry
- Quality Control
- Supply Chain Disruptions
- Resource Management
- Market Change
- Take the Leap—Supercharge Your Manufacturing with AI-Powered Services Today!
- FAQs
Introduction
Manufacturing is truly getting a serious makeover for the future, and it’s not full of buzzwords and techno-speak; with the dawning of AI technologies, manufacturing is no longer about nuts and bolts and conveyor belts.
Yes! We are talking about how Generative AI in manufacturing is transforming the entire industry.
It was the next secret sauce that made years, and the operational capabilities of factories turned upside down. From spearheading unparalleled automation advancement to mind-blowing design enhancements, AI has brought waves that have never been seen.
The statistics do not lie.
According to Precedence Research: U.S. generative AI in manufacturing market size was valued at USD 70.88 million in 2022 and is projected to surpass around USD 2,193.49 million by 2032, expanding at a CAGR of 41% between 2023 and 2032.
Billions of dollars in savings and monumental efficiency gains. Automated processes that self-correct, machines that learn and adapt, and designs that take minutes instead of weeks. Yeah, it’s that wild.
Stick with us if you want to be ahead of the curve and make some serious moves. Here are ten killer ways in which Generative AI transforms the manufacturing game for your business. Trust me, you’re going to want to ride this wave.
Generative AI in Manufacturing
Now, generative AI is beyond number-crunching or data sifting, as with traditional AI; it goes beyond all that. Unlike most other impostors, this one does a little more than recite history for you. It pulls in great swaths of data on real-time sensor inputs, product performance records, and even customer feedback to fashion ideal models and gives actionable recommendations.
This will lead to new product designs that GenAI can produce, optimize production, and predict what might go wrong, which will happen.
The outcome? Manufacturers can offer better stuff for less money, minimize waste, and offer bespoke solutions tailored to every customer’s unique needs while keeping innovation at the low cost of goods. It is like striking a goldmine in efficiency and creativity.
Key Features of Generative AI in Manufacturing:
Design Development: Deploying generative AI in manufacturing accelerates the development cycle with optimized designs or components, using data to do so.
Process Optimization: It fine-tunes the production process on the fly to keep operations humming at peak efficiency with minimal downtime and few hiccups.
Predictive Maintenance: Gen AI’s real-time machine crunching can predict when gear needs to be maintained. Therefore, surprise breakdowns that can throw a wrench in the works can be avoided.
Generative AI for Manufacturing: 10 Game-Changing Use Cases
Everyone’s talking about the new hot tech: Generative AI. This new hornet’s nest in tech has streamlined operations, reduced cost-cutting measures, and brought game-changing inventions that drastically transform the way manufacturing industries work. Now’s a good time if you’re in the manufacturing business and haven’t yet hopped onto the AI train.
Generative AI has high-end operational capabilities, but the key differentiator is how is Generative AI used in manufacturing.
To simplify things, we have decided to explain the real generative AI use cases in manufacturing. So, let’s get started with ten killer use cases for Generative AI in manufacturing.
Supercharging Product Design
Old Way: Waiting for paint to dry; that’s how it used to be, with a long list of approvals, iterations, and frustration.
New Way: Generative AI accelerates every design process, scooping data from previous projects at the speed of light and spitting out new design options. It relies on patterns, trends, and styles to quickly generate new, innovative ideas.
Results: Goodbye, old back-to-the-drawing-board routine. AI takes you from sketch to prototype faster, resulting in quicker turnarounds, new opportunities for innovation, and less revisiting of your design.
Also Read: How to Use AI to Design Better Mobile App User Experience?
Predictive Maintenance on Steroids
Old Way: Sit back and wait for your machines to break down, have costly repairs, have some unplanned downtime, and have a too-high bill. It was like sitting around waiting for disaster to strike, wasting away just time and money.
New Way: AI swoops in and takes charge. With real-time streaming data coming off your machines, AI can spot potential issues before they even happen. The digital standby crew checks in constantly with fingers on every piece of equipment that keeps your heads up before things go wrong.
How it Works: Sensors on your equipment send performance data 24/7 to the AI System. The AI system processes that data to identify patterns and alert you to potential impending issues, such as wear and tear or a decline in performance. You are immediately alerted and given time to troubleshoot the issue before it worsens. Bam! It’s already fixed before it happens!
Results: This system is like a crystal ball for your equipment. You will know about problems before they become problems, and there will be zero downtime, surprises, or headaches. Indeed, this game-changer makes operations run with fewer costly interruptions.
Demand Forecasting Done Right
Old Way: This was no feel-your-way affair. Flying blind, as it were, is the least to describe it. It is like this: You operate on instinct, pretty much a shot in the dark or by the seat of your pants. It’s the best guess that one can give with minimal information, but mostly, you will miss by a mile.
New Way: Finally, there’s AI, which spoils the party. After consulting over the history of sales, current market conditions, and general trends, AI provides a projection based on this information. It is just a crystal-clear roadmap of what’s ahead of you.
How it Works: AI sifts through every single form of data. Its content includes sales history, seasonality, and market trends. It calculates all of that to deliver accurate demand forecasts for smarter decision-making.
Results: With such accurate predictions, you will no longer have to overstock or understock and will have just enough stock to fill the demand. You will then be in a prime position to fill every order on time and avoid those expensive mistakes occasioned by over or under-ordering.
Also Read: How AI Powers Digital Transformation Across Industries
Custom Manufacturing
Old Way: Understanding the needs of each customer has always been dreadfully costly and agonizingly time-consuming. Therefore, Individualization took an eternity, was resource-intensive, and was impossible to scale beyond a tiny niche.
New Way: With AI, mass customization is effortless. Such technology produces configurations in products according to the customers’ demands without problems all at once; before, it was unimaginable and seemed to appear by clicking a button. It has speeded up and lessened costs for themselves.
How it Works: It won’t stop taking customer input in preferences or requests for certain products and producing like products. And it does all this without so much as a hiccup or evident slowdown in the work of any stage. Because the process is designed to flow smoothly and scale, you never lose your stride when running custom orders.
Results: Now, you can provide individually customized and personalized products with the speed and efficiency of mass-produced products. It is almost two worlds: ideal solutions for your customers are fully customized but with streamlined operations as in full-scale manufacturing.
Effective Supply Chain Management
Old Way: The worst thing is that managing your supply chain is like trying to herd cats. How the many moving suppliers and shipping logistics could keep everything running smoothly becomes a headache.
New Way: Insert AI to smoothen things out. AI does everything, from finding good suppliers that can be on the front line to searching for the best route to ship the said products. What once was a haywire and nerve-wracking task has now become smooth by machines with AI.
How it Works: All that number crunching is processed in real-time and determines logistics. It has identified the best supply and ensured optimum-level inventory; it can even help design shipping routes to use less time and reduce delay and cost.
Results: Consider AI as your internal GPS for your supply chain. It guides you through complexity without tension, smoothes the operation, and keeps you wallet-friendly by saving wasted time and other resources.
Quality Control On Track
The Old Way: Inspecting merchandise was a long, tedious process, slower than molasses. The human factor made it so that defects slipped by, and quality inconsistencies became standard.
New Way: AI quality control is great because it works like a pro. It quickly and accurately detects more errors than a human eye, ensuring that your final product is of the highest possible quality in every output. You can now let AI correct mistakes in the manufacturing line even before they leave.
How it Works: The AI scans every product image within a fraction of a second. At first glance, the algorithms flag any fault in their database, so only the best arrives at the market.
Results: Early detection saves waste and maintains quality. It’s an easy win-win: less waste, fewer returns, happy clients, and zero compromise on quality.
Smart Workforce Management
Old Way: Managing the labor is not an easy nut to crack. It is hard to understand what form of management over the workers is being implemented, what assignments are given, etc. It was not trackable in any respect.
New Way: AI shifts everything by automatically aligning the workforce and analyzing real-time data to ensure that labor is directed precisely where needed. It is like having an assistant who is always abreast of the latest news in the media, as the decision-making process is much smarter than even the most brilliant human being would be able to make almost instantly.
How it Works: AI senses the prevalent conditions and applies that intelligence to manage the workforce effectively. Therefore, shifts will be scheduled automatically, tasks will be assigned, and resource allocation will happen according to the immediate need of the operation. The AI constantly works out the right number of workers at the right location and task.
Results: AI workforce management is nearly an on-call digital foreman who is always ready and able to go, unlike human resources, which will make mistakes and punch the clock. Because of this, efficiency will skyrocket due to fewer scheduling conflicts, and the system will be much more productive and less prone to common human mistakes.
R&D Innovation Going Fast
Old Way: It was perceived as very costly and time-consuming. Validating new ideas, materials, or products could take months or even years before the change becomes effective. The old R&D model is expensive and time-consuming.
New Way: AI supercharges the whole R&D process. It can simulate thousands of “what if” scenarios within seconds, accelerating the innovation timeline. Companies can now explore possibilities in numbers they cannot achieve with physical prototypes or long testing periods.
How it Works: Researchers can simultaneously strive for new products and materials and approach design ideas. Through incredible speed, previously accumulated data fed to AI using predictive modelling will generate new ideas and solutions for the markets that streamline the whole cycle of R&D.
Results: You can create new inventions with little to no high R&D price tags. You can introduce new products in the marketplace faster while cutting orders of magnitude in research, testing, and development costs.
Automate Documentation and Compliance
Old Way: The old paper-based way of handling documents and compliance involved drowning in paper and, hopefully, scrolling through interminable lists. It took hours and was also prone to errors.
New Way: With AI doing all the heavy lifting, report generation and compliance tracking against all regulations will be automated. What might have taken hours by human hands now can be done in a tiny fraction of that time and much more accurately.
How it Works: They scan and process documents at warp speed, extracting all pertinent key data points and ensuring that everything passes under compliance standards. Whether you are scanning financial reports, regulatory filings, or internal documentation, AI can do it faster with a degree of accuracy impossible for humans.
Results: You spend fewer hours wriggling in the mire of paperwork and more hours doing high-level thinking—you’re running your business. You’re assured of timely documentation and compliance while using AI on the administrative side so that you can dedicate more of your time to the things that are important to you.
Energy Consumption
Old Way: Energy expenses have always been a steady pounder on your bottom line, slowly seeping away at your profit margin. Tracking and regulating energy usage was tough because most inefficiencies did not present themselves until they had built up.
New Way: AI recognizes anomalies that need to be reduced and gives actionable insights on reducing further energy use, thus saving money and resources.
How it Works: AI monitors machinery, lighting, and HVAC system usage patterns. It identifies areas where usage is not efficient or wasteful and provides ways to optimize usage by recalculating schedules, optimizing equipment settings, or initiating shut-offs during low usage.
Results: It saves the company money in terms of energy spent and contributes to helping sustain a greener environment. You save costs and help ensure this planet gets cleaned up better with AI in the energy sector. It saves money for you as a business owner while helping contribute to a greener environment.
Some Real-Life Examples of Generative AI in Manufacturing Industry
Conventionally, manufacturing industries must rely heavily on manual labor and human decision-making, which is subject to various risks and ultimately reduces productivity and efficiency.
However, the advent of AI in the manufacturing industry has completely transformed the operational landscape. Be it streamlining production lines, predicting pieces of equipment failures, or managing the workforce; generative AI is making significant strides. The deployment of generative AI has raised the number of intelligent factories.
Here are some real-life generative AI in manufacturing examples that show how industry leaders smartly inject super intelligence into every production line stage.
Predictive Maintenance
Companies like Rolls-Royce and General Electric (GE) are deploying the capability of AI-driven predictive maintenance, which allows their machines to anticipate failures before they occur. Let’s explore how they make use of Generative AI:
Rolls-Royce: As an aerospace and engineering company, Rolls-Royce sometimes encounters situations where it is unaware of the maintenance of its jet engine. Thus, it deploys generative AI to perform predictive maintenance to avoid this. Generative AI smartly analyzes the sensor data from test runs and predicts potential issues or risks associated with engines. This assists the company in planning the preventive measures promptly and assures complete safety.
Quality Control
Renowned automobile companies like BMW continuously assist their product enhancement vision through generative AI-powered systems and deep machine learning capabilities. With this advanced technology, the company not only surpasses human limitations but also inspects the product and makes it state-of-the-art innovation through exceptional accuracy and speed. Let’s explore how BMW employs Generative AI:
BMW: BMW targets those potential areas with the most minute flaws that are prone to risk and escaped by human detection. The possible areas could be sheet metal inspection or traditional defects like cracks. Along with the predictive inspection, generative AI capabilities save BMW’s time and resources by assisting them in wiping all the harmless blemishes from potential issues.
Production Optimization
Generative AI, with its algorithms, optimize workflow and resource allocation by smartly analyzing historical data and real-time production insights and metrics. However, this makes it easy for manufacturers to quickly identify bottlenecks and streamline the processes to avoid pitfalls related to production. Let’s see how companies like Honeywell leverage generative AI to facilitate production efficiency.
Honeywell: The company extensively employs generative AI to access data-driven production plans while considering utility costs, labor constraints, order deadlines, and inventory levels. Subsequently, this tech advancement allows the company to focus on enhancing operational strategies while elevating customer experience.
Key Benefits of Leveraging Generative AI for Manufacturing
Imagine machines that think, design, and solve anomalies faster than any human can. It’s not the setup for some sci-fi movie, but it’s true: Generative AI for manufacturing. Have you ever wondered how companies can roll out innovative products without downtime, reducing their negative impacts and gaining extra profits? The answer is that they are leveraging the advantages of generative AI in manufacturing.
Let’s explore the benefits of generative AI in manufacturing, which will rewrite the traditional manufacturing playbook.
Streamlined Designing
GenAI supercharges innovation. Iterative, painful design is out the window. GenAI is like a supercharged brainstorming buddy. Fed specs into its mouth; it spits dozens of product designs in seconds. So now you can figure out different prototypes much earlier than you’d have otherwise. It’s about things better, not things faster, and that’s a win!
Process Optimization
GenAI comes in, simulates each production process, and determines the most efficient ways of doing things. For example, you’d have that backstage pass to every possible scenario before that signal. You could catch bottlenecks, reduce waste, and optimize your workflow like a pro.
Predictive Maintenance
Of course, keeping machines running is critical, but now they can’t be maintained without being a pain. With traditional techniques, manufacturers will either wait for stuff to break down or over-maintain it – which isn’t very good and becomes some kind of money pit.
GenAI analyzes real-time performance data and can predict when something will go south. It’s become quite like having a crystal ball to your machines, preventing breakdowns from happening when they do. That means less downtime, fewer headaches, and way lower maintenance bills.
Data-Driven Decision Making
The most eye-catching of all the benefits of generative AI in manufacturing is that it can drive data-driven decision-making, which is a game-changer in determining and sustaining success.
GenAI is like that wise old business mentor who never sleeps. Learning and analyzing the data gives manufacturers insights into making lightning-fast, well-informed decisions. Whether shifting gears in the face of jarring market changes or shifting production to fulfil customer demand, manufacturers now have an upper edge by keeping agility and responsiveness on their side.
Also Read: Big Data in Manufacturing – Importance and Use Cases
Sustainability Improvements
The combination of AI and Sustainability isn’t good for the earth-it’s good for business, too. With GenAI, a maker can make things greener by optimizing materials and design to reduce waste and carbon footprint. It’s all about building smart products without loss of performance. From slashing material use to amplifying power efficiency, GenAI makes cutting waste much easier and easily ratchets up your eco-game.
Also Read: What is The Potential Impact of Generative AI on Industries?
How to Implement Generative AI in Manufacturing Workflow?
Introducing generative AI in the manufacturing industry or workflow doesn’t happen overnight or automatically. A structured approach is required to gain maximum benefit from the technology. It is advisable that before starting with the implementation of generative AI in manufacturing, you must understand the precise role of generative AI in manufacturing.
For your ease, here is a step-by-step disintegration so you understand how to introduce it into your system without any hassle or muss:
Gather all the data
Data is the lifeblood of any AI system. Start by collecting all the data from nearly every source, from source to destination and the entire production chain. These would range from machine sensors, logging performance, and operational conditions to production logs, which record how things are made; then, customer demand patterns, market trends, and even supply chain insights and competitor movements.
The more data you can aggregate, the better your AI will be at making accurate predictions and generating valuable insights. Consider this step akin to the foundation of a house: the stronger the foundation, the more likely the entire house will function properly.
Cleanse Your Data
This is like pre-preparing ingredients before cooking; if your vegetables haven’t been chopped right or your spices haven’t been measured correctly, the final dish will taste bad. Properly formatted and clean data will enable the AI model to yield better results.
Now that you have it, you can start cleaning up your data. Raw data typically has errors, or information is inconsistent and not relevant. Generative AI needs clean data for the model to work well or be correctly formatted. The process of filtering out “noise”-in this sense, data that are not helpful or incorrect is organized into an easy structure for the AI model to process end.
Train Your AI Model
That’s where the magic happens. The generative AI learns patterns, trends, and relationships with historical data. After that, the model is ready to help predict future outcomes and generate new solutions—whether that means optimizing the use of machinery, reducing downtime, or coming up with completely brand-new product designs you wouldn’t have thought of otherwise.
For instance, maybe it helps you design a new component that’s much more efficient, cheaper to produce, and longer-lasting than you are using now. Or it predicts when a machine will likely fail so you can fix it before it breaks down and you have expensive production stops. In short, you are giving the AI enough experience to make it an expert in manufacturing processes.
Plug It Into Your Systems
The AI model is only useful if integrated with your other manufacturing systems. Nobody wants the AI to run in a vacuum, so it must communicate with your usual software and hardware tools. Perhaps it should link your production management system, provide supply chain logistics, or track your inventory.
Synchronizing AI with operational infrastructure can infer real-time insight. This ensures you can make instant decisions based on the AI’s predictions.
Keep Learning, Keep Evolving
AI’s most significant advantage is that it is not static; it learns continuously. The more data it receives, the smarter it becomes. That is to say, you will need to keep feeding it new data so it can continue changing with your business. This process is called continuous learning, and it’s key to maintaining a competitive edge.
The more knowledge your AI accumulation absorbs, the better its predictions will be and the more rational its processes in optimization will be. If market conditions change or you launch a new product line, your AI will adapt and provide you with new insights for that adjustment.
What are the Challenges with the Adoption of Generative AI in Manufacturing Industry
Seriously, running a manufacturing operation comes with a long list of challenges. Bottlenecks in the supply chain, skyrocketing production costs, and the need to constantly innovate can sometimes feel like juggling chainsaws. While adopting this new technology, you might encounter various challenges related to generative AI in the manufacturing industry.
However, generative AI in the manufacturing industry invades the playing field to flip this script. Whether optimizing production lines, demand prediction, or personalized products at scale, this was and is cutting-edge technology. And it wasn’t a game of keeping up but of getting ahead.
Explore how Generative AI in the manufacturing industry is tackling manufacturing’s headaches.
Quality Control
Quality in the final product is always a great manufacturing challenge because traditional quality control methods, such as manual inspections, rarely find fine defects. Thus, defective products, higher return rates, and damage to brand reputation result.
Solution: Generative AI performs real-time quality control for products and detects defects while producing, resulting in fewer defective products, an increase in customer trust, and a reduction in return rates.
Supply Chain Disruptions
Supply chain disruptions, such as delayed orders or unavailable raw materials, can throw production schedules off track, leading to missed deadlines and added expenses.
Solution: Generative AI’s forecasting models predict the chances of supply chain disruptions and offer other options, including modifying production schedules and using different resources, even new suppliers, to minimize operations’ downtime and expensive delays.
Resource Management
Mismanagement causes inefficient resource utilization, which results in inefficiencies and inflated operational costs. Traditional approaches often result in either overuse or underuse of equipment and labor.
Solution: Generative AI in the manufacturing industry supports predictive maintenance, equipment requirements prediction, and workforce deployment optimization. It reduces downtime, extends machinery life, and increases productivity while reducing waste.
Market Change
Rapid changes in consumer preference and market trends can be disastrous for manufacturers. They can lead to unsold inventories or a loss of market share.
Solution: Generative AI for manufacturing can analyze market trends and real-time customer feedback. This way, manufacturers can adapt faster. That means they would stay on the competitive edge with consumers’ demands while avoiding outdating their products.
Take the Leap—Supercharge Your Manufacturing with AI-Powered Services Today!
So far, you must understand and visualize the change that AI will bring to your manufacturing arena. So, if you are looking for AI-based IT solutions for manufacturing, Appinventiv is a name to be reckoned with as the top global Generative AI consulting company. From predictive maintenance to seamless supply chain management, our bespoke services not only cut downtime but also ensure a level of quality control that empowers you to stay ahead in the manufacturing game.
Don’t get left in the dust. Complete this form and start building something extraordinary together. Whether you’re after streamlined supply chains, automated quality control, or groundbreaking product innovation, we are here to make it happen.
Your future in manufacturing starts here. Let’s create it.
FAQs
Q. How does Generative AI differ from traditional AI in manufacturing?
A. Generative AI is the latest version of the traditional approach that emphasizes data analysis and pattern recognition. Using extensive data sources such as sensor inputs, product performance records, and customer feedback generates new designs, optimizes production processes, and offers real-time insights for manufacturing companies to innovate more quickly, waste less, and spend less.
Q. What is the future outlook for Generative AI in manufacturing?
A. The future for the Generative AI market in manufacturing across geographies is bright since it is expanding further with a projected CAGR of 41% from 2023 to 2032. More and more manufacturers are incorporating AI-driven tools in designing, maintaining, and producing optimum outputs. Therefore, this technology would play a huge role in redefining the future of this industry.
Q. How does Generative AI improve predictive maintenance in manufacturing?
A. Generative AI analyzes real-time data from machinery to predict when maintenance is due. It identifies possible problems before they are translated into equipment failures; hence, it reduces unplanned downtime, lowers maintenance costs, and ensures smoother processes in production.
Q. Can small manufacturers benefit from Generative AI, or is it only for large companies?
A. The forces of generative AI will be in the hands of small or large manufacturers. Smaller companies will use it to lower waste, streamline operations, and improve production efficiency, thus making it less of a discriminator in an intensely competitive manufacturing environment.
Q. What are the key use cases of Generative AI in manufacturing?
A. Some of the highest use cases are supercharging product design, producing techniques in optimized processes, predictive maintenance, improved demand forecasting, personalized manufacturing at scale, and better management of supply chain resources. All these applications help manufacturers be efficient and cut their costs to be competitive.
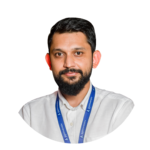
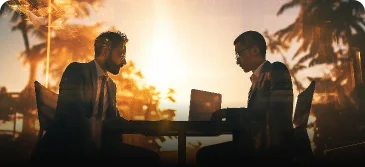
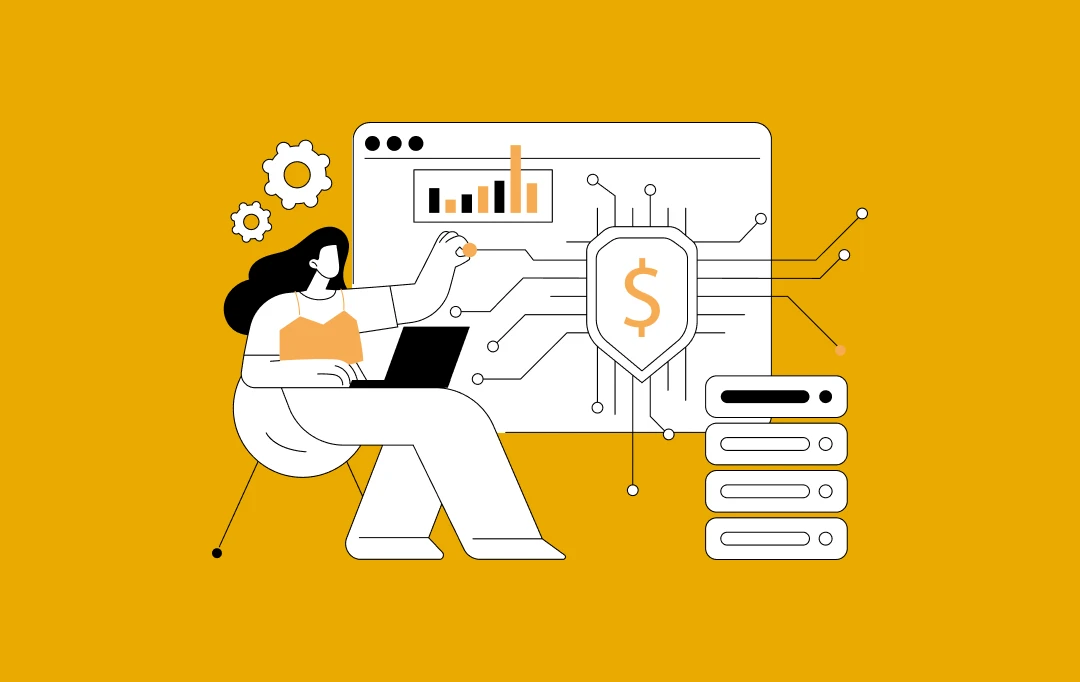
How Much Does it Cost to Build a Custom AI-based Accounting Software?
The accounting industry has been evolving very fast, and the expanding use of AI in accounting is becoming evident. According to The State of AI in Accounting Report 2024, 71% of accounting professionals believe that artificial intelligence in accounting is substantial. Considering the given number, it is easy to grasp why companies are keen on…
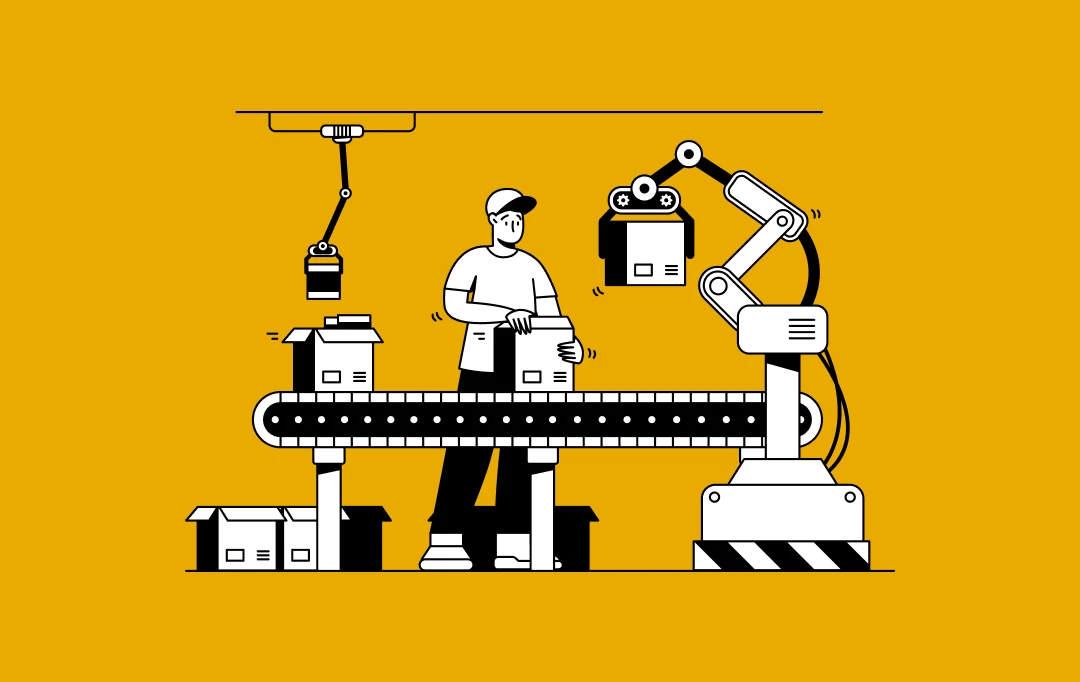
10 Use Cases of Computer Vision in Manufacturing: What Revolution Can the Industry Expect?
The transformative phenomenon of Industry 4.0, born from the demands of resource and energy efficiency, urban production, and demographic changes, continues to shape the future of manufacturing. With its focus on automation, predictive maintenance, and process optimization, the digitalization phase brought in a new level of efficiency and responsiveness. And just when manufacturing units were…
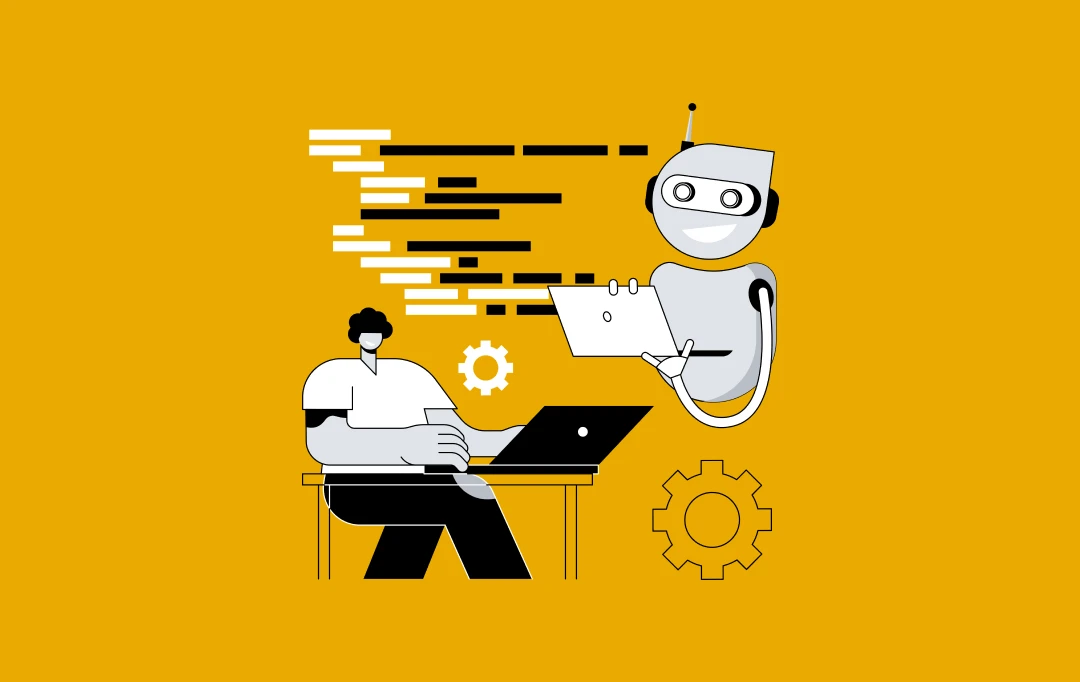