- IoT: An attempt to bring Digital transformation in manufacturing industry
- Why is IoT gaining traction in 2024 and beyond?
- Adoption of Industrial Internet of Things in the manufacturing industry
- 1. Cost reduction
- 2. Mass customization
- 3. Shorter time to market
- Benefits of IoT in manufacturing and related industries
- 1. Asset tracking
- 2. Facility management
- 3. Enhanced machine utilization
- 4. Predictive maintenance
- 5. Connecting remote assets
- 6. Process and behavior monitoring
- Components of IoT
- Smart assets
- Data communication infrastructure
- Software and analytics
- People
- Real-time examples of IoT in manufacturing
- Supply Chain Optimization
- Energy Management
- Machine monitoring to track OPE/OEE
- Inline quality assurance
- Poka-Yoke
- Challenges of IoT adoption in manufacturing and business
- To Wrap it up!
- FAQs
- Q. What is the use of IoT for manufacturing?
A few years ago, IT experts declared that digital technologies could not influence specific sectors. But here we are, harnessing every single field with digital power. What made all of this possible? Consumer interests and their demand for customization have driven the rise of IoT.
What is IoT? It’s the biggest attempt to bring digital transformation.
IoT (Internet of Things) describes the network of physical objects embedded with software, sensors, and other technologies to connect and exchange data with systems and devices over the internet. These devices range from your everyday objects to industrial tools.
If you wear fitness trackers such as FitBit or use voice assistants such as Alexa or Siri, you probably know what IoT is. By 2025, over 75 billion devices are projected to be connected via IoT.
IoT: An attempt to bring Digital transformation in manufacturing industry
IoT or the Internet of Things has already broken all possible online barriers by interconnecting various technologies and bringing them under one umbrella. The statistics presented by MarketsandMarkets state that the global IoT in manufacturing market is expected to grow from $50 billion (2021) to $87.9 billion (2026), witnessing a CAGR of 11.9% from 2021 to 2026.
This growth is due to the rising need for centralized monitoring, maintenance of manufacturing infrastructure, and worldwide adoption of cloud services.
With these promising figures, implementing IoT services in businesses and the manufacturing industry is the best way to bring digital transformation.
Also Read: AI in Manufacturing – Use Cases and Examples
Why is IoT gaining traction in 2024 and beyond?
IoT solutions are already helping businesses with scheduling predictive maintenance, collecting data, and in 2024 we will continue to see organizations enhancing their operations using IoT.
If you ask, what makes IoT so special? Here’s the answer.
Three major technologies empower IoT –
There is hardly a segment that runs without the above technologies. Be it agriculture, smart city, robotics, healthcare, retail, or home automation. IoT is a broad use case that covers everything from using public cameras for monitoring social distancing to using telemedicine and remote healthcare.
You may also like IoT in Fintech – How It’s Transforming the BFSI Market
Speaking of which, the IoT in manufacturing industry, often referred to as IIoT (Industrial Internet of Things) has vast implications on operations. This covers how we manufacture goods, sell to customers and follow up with support. The integration of IoT infrastructure and robotics within manufacturing processes is paving the way for companies to leverage IoT in ushering in the era of Industry 5.0. This evolution highlights IIoT as a pivotal driving force, marking the significant leap from Industry 4.0 to embracing Industry 5.0 in manufacturing. This brings us to our next point of discussion.
Adoption of Industrial Internet of Things in the manufacturing industry
Before you confuse IoT (Internet of Things) with IIoT (Industrial Internet of Things), here’s a clarification:
IIoT (Industrial Internet of Things) is a subcategory of IoT (Internet of Things) used in an industrial context. It’s a unique phenomenon where various digital tools are used to connect data and machines in “smart factories” for productivity and quality.
Therefore, IoT is a consumer-centric concept, whereas IIoT is more focused on supply chain, manufacturing, and management.
Coming back to the adoption of IoT, the expectations are much higher when it comes to the manufacturing industry. There is a robust and never-ending demand for steady growth and personalization along with supply complexities. Besides all these challenging needs, enterprises, manufacturers, and product producers are looking for extraordinary ways to compete and lead the market.
Apart from the above reasons, three significant factors explain how IoT helps in manufacturing.
1. Cost reduction
Manufacturers tend to use IoT due to efficient inventory management, agile operations, and reduced operational costs. For example- smart connected products allow you to analyze from selling products to selling experience. This means you have a watch on product usage as well as post-sale service.
2. Mass customization
This is probably one of the biggest factors to use IoT. The process of mass customization requires an increase in various products and tools, which results in diverse inventory. These operations are complex and require a feasible solution. IoT facilitates mass customization and acts as a real-time data source through scheduling and forecasting.
3. Shorter time to market
When manufacturing is faster and efficient, the product cycle time reduces. Take the example of Harley-Davidson. It used IoT to reconfigure its York and improved its manufacturing facility, which reduced the total time of creating one bike from 21 days to 6 hours.
You can explore more real-time IoT cases here, 5G and IoT: Emerging technologies with endless use cases.
Benefits of IoT in manufacturing and related industries
Now that we know how IoT technologies are a game-changer for manufacturers, let’s see how this actionable data benefits manufacturers and other related industries. The organizations can break open the given data silo and access information at any level. This way, engineers, operators, and supervisors can easily gain visibility into production. They can take cues from the machine data and improve efficiency on the production floor.
Moreover, businesses can make more informed decisions that are backed up by data. So overall, personnel at all levels can detect problems and optimize operations using the Internet of Things.
You also get the following benefits from IoT.
1. Asset tracking
You can track products throughout the supply chain and notify the stakeholders of caution and possible damage to the goods.
[Also Read: Smart Railways – How IoT is Transforming Train Travel and Operations]
2. Facility management
IoT-connected sensors and tools can examine conditions like humidity, temperature, and vibrations. They can easily detect conditions that can negatively affect operations and alert you beforehand.
3. Enhanced machine utilization
The Industrial Internet of Things enables connecting machines to the internet, giving you an insight into machine lifelines and KPIs. This data is a massive help in fixing the causes of unplanned downtime.
4. Predictive maintenance
Real-time data from interconnected IoT devices help predict defects in tools and machinery. This again saves you downtime and helps increase the overall productivity.
Not to forget the associated cost you save by reducing process time, scrap, and rework.
5. Connecting remote assets
Connecting tools and devices means that data from various remote assets are easily accessible from one central location. These assets can be examined and monitored, giving you a higher degree of control.
6. Process and behavior monitoring
In business organizations and enterprises, managers can gain insight into their employees’ performance using IoT data. For instance, one can identify that employees consistently produce defections due to this step and perform a root cause analysis. This translates to quality assurance, cost-saving, and enhanced scalability.
[Also Read: IoT In Logistics And Supply Chain – Benefits, Use Cases & Challenges]
Components of IoT
Enough about the benefits of the Internet of things in manufacturing, you might now want to know how IoT works. In order to understand how IoT functions, you need to look into its components.
The Industrial Internet of Things links smart assets, a data communication infrastructure, software and analytics, and lastly, the people. This connection generates actionable data for manufacturing and operations.
Smart assets
These smart or intelligent assets contain interconnected things like devices, security components, application software, controllers, etc. These modern assets have communication capacity with local intelligence, and they support analytics with connectivity and provide you with information for the value chain.
Examples of intelligent assets in IIoT
- Digital equipment
- Plants instrumentation
- Edge devices
- Embedded systems
Data communication infrastructure
The smart assets in the IIoT system need other technologies and the internet to establish communication. Nowadays, Industrial IoT systems are deployed on cloud infrastructures like Amazon Web Services. These infrastructures store, manage and process data using remote servers.
Software and analytics
IoT software analyzes the data collected by the devices and systems. It also gives you an interface to interact with other systems.
Cloud-based software provides unlimited limited benefits to manufacturers over on-premise software. This gives greater speed, flexibility, and reliability. Read how IoT helps manufacturers better their operational efficiencies.
People
This one is an important and, unfortunately, the most overlooked component of IIoT. People interact with the system by making decisions based on data and analysis. The better the data, the better the decisions. Hence, a quantified balance is maintained in the organization with the interaction between people and other IoT components.
Related article: Demystifying IIOT – 10 Applications and Use Cases across Industries
Real-time examples of IoT in manufacturing
You are all set to implement IoT in manufacturing with the above components. The use cases of IoT are ever-expanding; this being said, below are some of the real-time IoT use cases you can relate to.
Supply Chain Optimization
One of the most notable examples of the Internet of Things in manufacturing is optimized supply chain management. IoT aids in tracking inventory levels, monitoring logistics, and streamlining the entire supply chain process.
Energy Management
IoT systems monitor and optimize energy usage across manufacturing facilities, identifying areas of excess consumption and implementing energy-saving measures to reduce overall operational costs.
Machine monitoring to track OPE/OEE
You can track Overall Process Effectiveness (OPE) and Overall Equipment Efficiency (OEE) through collected data on machine uptime. This allows you to gain visibility and monitor state data. This can be done using sensors connected to IoT gateways.
Inline quality assurance
You can also use smart assets such as scales, calipers, machine vision cameras at quality check departments. Intelligent sensors give a more accurate precision than any manual inspection device. Even better, you can install quality checkpoints throughout the production process to catch defects early.
Poka-Yoke
Poka-Yoke is a popular manufacturing technique that means “mistake-proofing.” For instance- using IoT scales to detect a product’s weight. If it’s out of specification, it signals a mistake.
If this makes you interested in implementing IoT in your next project, you can check out how to make your IoT project successful for better insights.
Challenges of IoT adoption in manufacturing and business
So far, we have discussed all the good the Internet of Things brings to your business. It’s time we also get familiar with a few of the challenges it brings.
According to a BCG survey, the toughest challenges faced by US enterprises include data security and privacy issues, lack of qualified systems, uncertainty about ROI, etc.
Let’s take a brief look at them.
- Data security/privacy issues
Major IIoT adopters believe the concept is increasing the risk of cyberattacks. As IoT systems have started becoming more commonplace, Forbes says, each IoT device represents an attack surface that can be an avenue into your data for hackers. If you want to know more about maintaining security in the IoT era, read how to ensure cybersecurity in the age of IoT.
- Uncertainty in ROI
IoT asks for several investments like hardware expense (sensors, gateways), cloud storage expense, cost of connectivity and administrative labor, etc. Businesses and industries have to consider quick solutions to generate a good ROI.
- Lack of qualified system
Prominent industry experts state that most of their employees are unfamiliar with IoT usage. Few similar surveys say that the system lacks specific skills such as embedded data, electronics, Big Data, and IoT security.
To Wrap it up!
To summarize, the Industrial Internet of Things in manufacturing and businesses helps maximize productivity, reduce cost, and eliminate waste. By leveraging IoT technologies and data, you get a better understanding of demand forecasting and supply chain process that ultimately results in a better customer experience. Hence, it’s never too late to seek IoT software development services for your business.
Appinventiv, as a trusted manufacturing IT services & solutions provider can help you with IoT consultancy, IoT app development , wearable connectivity development along with testing and maintenance. With advanced and proficient skills, we have contributed to scaling many businesses’ productivity and scalability. Let’s see what we can do for you. Connect with us!
FAQs
Q. What is the use of IoT for manufacturing?
A. There are various uses of IoT for manufacturing; for instance:
- IoT solutions for manufacturing enable continuous tracking of production processes and machinery, allowing for immediate detection of issues.
- The technology streamlines production lines by automating tasks, increasing efficiency and consistency.
- IoT uses data analytics to predict equipment failures before they occur. It helps improve equipment lifespan and reduce downtime.
- One of the most remarkable uses of IoT in manufacturing is optimized supply chain management, which improves inventory tracking, demand forecasting, and logistics.
- IoT in the manufacturing industry enhances operational efficiency and reduces operational costs through better resource management.
Q. What problems does IoT solve in manufacturing?
A. IoT in the manufacturing industry solves various problems on the factory floor and addresses challenges, including:
- Equipment downtime
- Energy inefficiency
- Lack of visibility in production processes
- Lack of qualified system
- Data security and privacy issues
Q. What are the future trends of IoT in the manufacturing industry?
A. The future of IoT in manufacturing is redefined by the integration of various technologies like
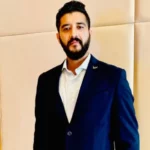
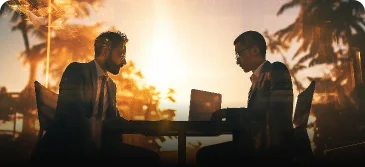
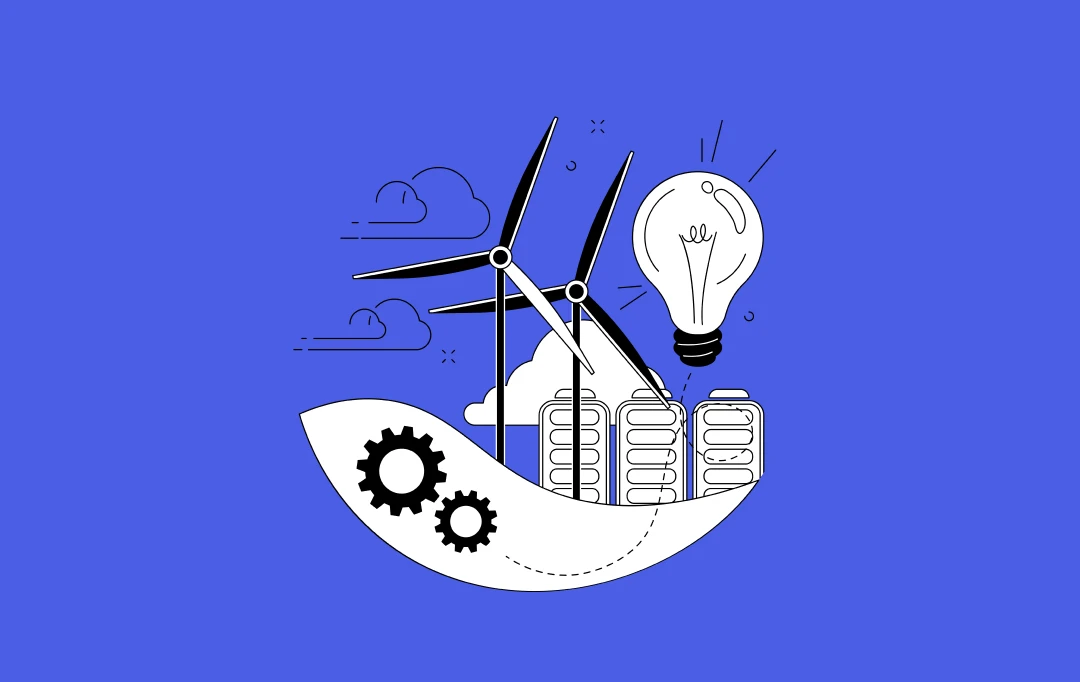
Top 10 Use Cases and Benefits of IoT Energy Management Changing the Power Industry
The escalating demand for energy consumption worldwide is projected to reach around 800 exajoules by 2050, a big jump from over 600 exajoules in 2019. This fastest-growing global energy use is throwing a major curveball - prioritizing smart energy for waste management. In this pursuit, the rise of the Internet of Things (IoT) offers a…
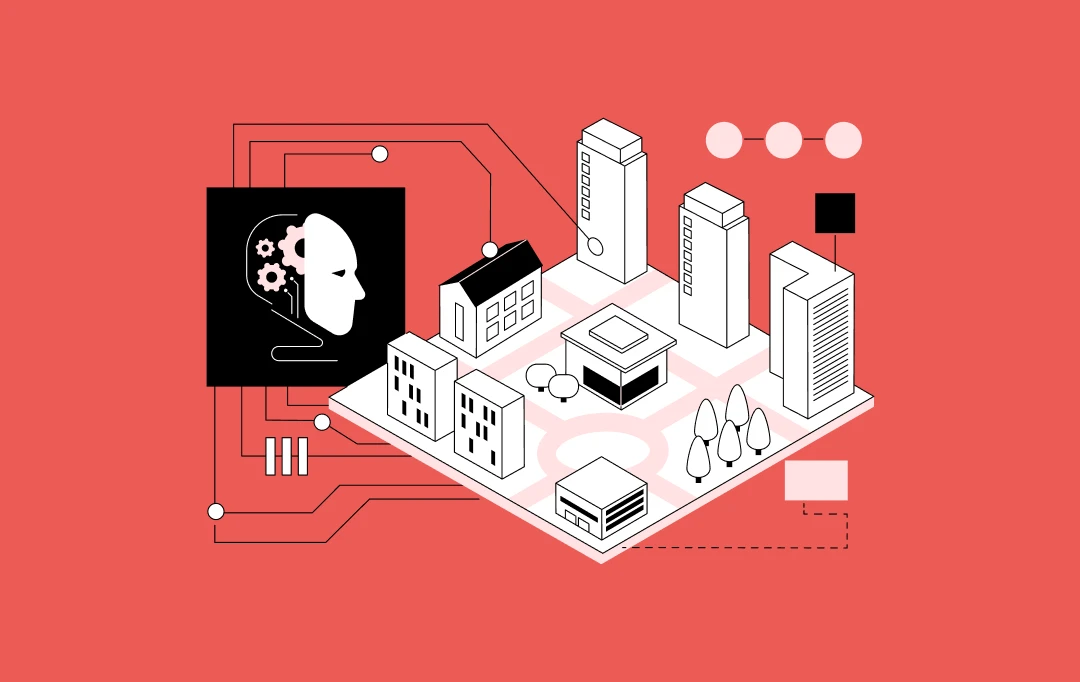
IoT in Construction: 10 Transformative Use Cases and Their Impact
The construction industry has always been the backbone of our infrastructure, but it hasn't always been quick to adopt new technology. Nevertheless, this fact is changing with the evolution of the Internet of Things (IoT). IoT has moved beyond being just a buzzword to a fully integrated tool transforming how construction projects are planned, executed,…
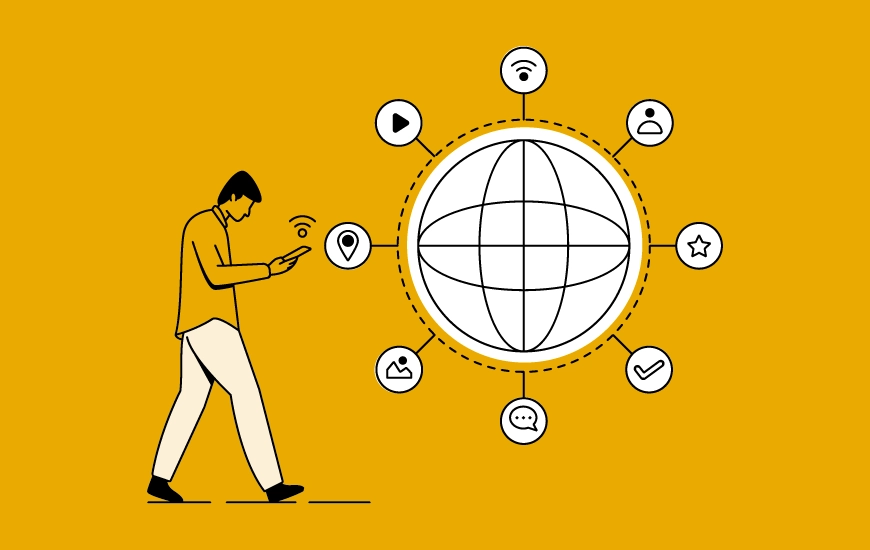