- What is Industry 5.0 in the Manufacturing Industry
- Businesses Benefits of Industry 5.0 in Manufacturing
- Increased Efficiency and Productivity
- Enhanced Quality Control
- Improved Safety
- Cost Reduction
- Sustainable Manufacturing
- Industry 5.0 Technologies and Their Remarkable Use on the Factory Floor
- Collaborative Robotics (Cobots)
- Artificial Intelligence (AI) and Machine Learning (ML)
- Internet of Things (IoT)
- Augmented Reality (AR) and Virtual Reality (VR)
- Digital Twins
- Additive Manufacturing (3D Printing)
- Challenges and Solutions to Implement Industry 5.0 in Manufacturing
- Workforce Adaptation
- Data Security and Privacy
- Interoperability and Standardization
- Ethical Considerations
- Future of Industry 5.0 in Manufacturing
- Ensure a Smooth Transition from Industry 4.0 to Industry 5.0 with Appinventiv
- FAQS
Industry 4.0 has benefited the industry for over a decade, and now it is time for Industry 5.0 in manufacturing. Industry 4.0, the fourth industrial revolution, has offered endless opportunities for enterprises in mass production, efficiency, interconnection, digitalization, massive data collection, automation in the manufacturing industry, and the ability to customize any part of the production line.
However, despite all these gains, Industry 4.0 has certain limitations and shortcomings. In today’s competitive age, workers in manufacturing and other industries often feel undervalued, with their roles often leaning towards supervisory responsibilities. They don’t have direct involvement in the manufacturing process to meet the ever-evolving users’ preferences and market demands for speed, security, and customization.
Industry 5.0, the next industrial revolution, aims to address these challenges by synergizing human creativity with mechanized efficiency. In Industrial Revolution 5.0, robots understand human cognition and work in collaboration rather than competition. Instead of eliminating the complete involvement of humans in the manufacturing process, it further integrates workers into production processes by leveraging their intuition, skills, and ability to solve problems creatively.
Therefore, the concept of industry 5.0 manufacturing enhances its predecessors by refocusing the workers’ role at the factory’s heart and building close interaction between humans and machines.
Let’s delve deeper to understand the manufacturing 5.0 revolution, its benefits, challenges in its successful adoptions, and the future of human-centric industry 5.0 in this transformative era.
What is Industry 5.0 in the Manufacturing Industry
In today’s fast-paced business landscape, staying ahead means embracing the cutting edge of technological evolution, and this is where Industry 5.0 shines. This next phase of industrial innovation is not just about machines but about revolutionizing the factory floor that works on three core principles: human-centeredness, sustainability, and resilience.
Sustainability: Industry 5.0 is committed to sustainable practices that minimize environmental impact and promote long-term ecological balance. Through the optimization of resource usage, energy efficiency, and waste reduction, the manufacturing 5.0 revolution helps embrace sustainability, contributing to a more resilient and environmentally conscious future.
Resilience: In the face of evolving challenges such as the COVID-19 pandemic, global shortages of supplies, natural disasters, and geopolitical instability, Industry 5.0 prioritizes resilience. It prioritizes building manufacturing systems that are adaptable, flexible, and capable of withstanding disruptions. By leveraging advanced technologies and agile production processes, Industry 5.0 equips businesses with innovative solutions that help navigate uncertainty.
Human-Centeredness: This fifth industrial revolution emphasizes the importance of human interaction, ingenuity, and collaboration alongside the power of smart machines and cutting-edge technologies. By fostering collaboration between humans and machines, Industry 5.0 seeks to enhance workplace safety, job satisfaction, and overall quality of life for workers.
According to different studies conducted in the manufacturing sector, human workers have confirmed that 71% of their daily jobs are either dangerous, dull, or dirty. Also, over 80% of these workers have reported sustaining injuries while on the job.
This is where Industry 5.0 emerges as a trusted savior, offering a symbiotic relationship between humans and machines to tackle physically demanding tasks safely while empowering workers to focus more on value-added activities.
Imagine you work in a production line and are required to assemble a product that needs several heavy parts. So, instead of hurting your back and shoulders to carry a big metal piece, you can leverage the advantages of robotic hands that will do all the heavy lifting for you.
You can also have a Cobot by your side, miming your movements with additional thinking, protecting you from getting injured in an unsafe environment. These Industry 5.0 examples show how machines don’t replace humans but collaborate and evolve together.
Businesses Benefits of Industry 5.0 in Manufacturing
Industry 5.0 brings a host of benefits to manufacturing processes, workers, and society as a whole. Let’s delve into the advantages of Industry 5.0 for manufacturing industry growth in detail:
Increased Efficiency and Productivity
By leveraging advanced technologies such as AI, IoT, and robotics, businesses can optimize production processes, reduce downtime, and enhance overall efficiency. This optimization allows human workers to concentrate on more complex and value-added activities, leading to increased productivity levels.
Also Read: What is production efficiency in manufacturing and how to achieve it?
Enhanced Quality Control
AI-driven quality control systems can easily analyze vast amounts of data in real-time, facilitating the detection of defects and deviations from specifications. Moreover, IoT sensors provide continuous monitoring of production parameters, enabling early detection of potential quality issues and reducing the likelihood of defective products reaching consumers.
Improved Safety
Industry 5.0 plays a pivotal role in ensuring safety in the manufacturing industry. Collaborative robotics and AI-powered predictive maintenance systems help identify and mitigate safety hazards in the manufacturing environment. Also, AR and VR technologies offer immersive training experiences and virtual simulations, providing workers with a safe environment to practice hazardous tasks.
Cost Reduction
Industry 5.0 contributes to cost reduction. AI-driven optimization and predictive maintenance help minimize downtime, extend equipment lifespan, and reduce maintenance costs. Furthermore, additive manufacturing technologies enable the on-demand production of spare parts and customized components, reducing inventory costs and eliminating the need for extensive warehousing.
Sustainable Manufacturing
Industry 5.0 fosters eco-friendly practices and resource-efficient processes, contributing to environmental sustainability goals. Optimization of resource usage and energy efficiency through AI-driven algorithms and IoT-enabled monitoring systems reduces environmental impact. Also, additive manufacturing processes generate less waste than traditional manufacturing methods, leading to a more sustainable approach to production.
You may like reading: How AI, IoT, and AR/VR Help Companies Achieve Their Sustainability Goals
Industry 5.0 Technologies and Their Remarkable Use on the Factory Floor
Industry 5.0 drives evolution in manufacturing by integrating advanced technologies with human-centric approaches to improve efficiency, productivity, and safety on the factory floor. Here are some key technologies associated with Industry 5.0 and their applications:
Collaborative Robotics (Cobots)
Cobots are designed to work alongside humans, enhancing productivity and safety. They are efficient at performing tasks that are physically demanding, repetitive, strenuous, or dangerous, freeing up human workers for more complex or creative tasks.
They are widely used for pick-and-place operations, assembly, quality inspection, and material handling. Cobots can adapt to various production processes and collaborate with human workers without needing any safety cages.
For example, BMW has integrated cobots into its manufacturing processes to enhance efficiency and boost productivity. These cobots work diligently with human employees, helping them with physically demanding and repetitive tasks.
Artificial Intelligence (AI) and Machine Learning (ML)
AI and ML algorithms analyze vast amounts of data to optimize production processes, predict equipment failures, and improve quality control. AI-powered predictive maintenance can anticipate equipment breakdowns before they occur, reducing downtime and maintenance costs.
Furthermore, ML algorithms can optimize production schedules, inventory management, and supply chain logistics, leading to more efficient resource allocation and reduced waste.
Related Article: Role of AI in Manufacturing: Use Cases and Examples
Internet of Things (IoT)
IoT devices and sensors collect real-time data from machines, equipment, and processes, providing valuable insights for manufacturing operations, remote monitoring, and optimization.
These insights enable manufacturers to identify inefficiencies in equipment performance and implement corrective actions. IoT in manufacturing can detect anomalies in machine behavior and alert maintenance teams to address potential issues before they escalate.
Augmented Reality (AR) and Virtual Reality (VR)
AR and VR technologies enhance worker training, maintenance, and troubleshooting processes by providing immersive, interactive experiences.
AR overlays digital information onto the physical environment, assisting employees through complex tasks, such as equipment setup, maintenance procedures, or quality inspections.
VR enables employees to practice operating machinery in a virtual environment, minimizing the risk of accidents and improving skills proficiency.
Digital Twins
Digital twins hold immense potential for revolutionizing manufacturing operations, enabling manufacturers to simulate, analyze, and optimize their operations in a virtual environment. By creating virtual replicas of physical assets, processes, and systems, manufacturers can gain deep insights into machine performance, predict maintenance needs, and identify opportunities for improvement. By leveraging the power of digital twins, businesses can unlock new levels of efficiency, agility, cost reduction, and innovation, ultimately attaining success in the Industry 5.0 era.
Additive Manufacturing (3D Printing)
3D printing is a crucial component of human-centric manufacturing, enabling the production of three-dimensional objects layer by layer and offering unrivaled flexibility in the production process. This revolutionary technology redefines prototyping, customization, and small-batch production by enabling on-demand manufacturing of complex components.
This industry 5.0 manufacturing technology reduces lead times, material waste, and tooling costs compared to traditional subtractive manufacturing methods. Also, it enhances human-machine manufacturing as employees can integrate their creative skills into product design, while 3D printing turns these ideas into reality.
By seamlessly integrating these advanced technologies, Industry 5.0 empowers workers, enhances productivity, and drives innovation on the factory floor.
[Also Read: Digital Transformation: What Manufacturers Need to Know about the Imperative Change]
Challenges and Solutions to Implement Industry 5.0 in Manufacturing
As more and more businesses are increasingly embracing the manufacturing 5.0 revolution, it is easier to overlook the potential challenges. However, organizations must identify and resolve the challenges efficiently for the growth of the manufacturing industry.
Workforce Adaptation
Challenge: The implementation of human-centric Industry 5.0 technologies requires a workforce with new skill sets to work with advanced robots and smart machines.
Solution: Organizations need to invest in workforce training and education programs to upskill existing employees and prepare the next generation of workers for future jobs.
Data Security and Privacy
Challenge: Increased connectivity and data exchange in Industry 5.0 raise concerns about the protection of sensitive information and cybersecurity threats.
Solution: Businesses must implement robust cybersecurity measures, encryption protocols, and access controls to ensure data security and privacy.
Interoperability and Standardization
Challenge: Integration of diverse technologies and software solutions may lead to compatibility issues and interoperability challenges.
Solution: Manufacturers should develop industry-compliant solutions that guarantee seamless communication and interoperability between devices, machines, and software platforms.
You may like reading: Compliance Management Software Development – Benefits, Use Cases, Process and Costs
Ethical Considerations
Challenge: The widespread adoption of AI, automation, and robotics raises ethical concerns related to job displacement, algorithmic bias, and data misuse.
Solution: To address this challenge, businesses should follow ethical guidelines, regulatory frameworks, and oversight mechanisms to ensure the responsible deployment of Industry 5.0 technologies.
Future of Industry 5.0 in Manufacturing
The future of Industry 5.0 in manufacturing holds immense promise, driven by ongoing technological advancements, changing consumer demands, and evolving global trends. It will foster deeper collaboration between humans and machines, enhancing productivity, safety, and flexibility on the factory floor. Industry 5.0 will enable the mass customization of products, catering to the evolving customer preferences and market demands through agile and adaptive production systems.
The differences between factories today and factories in 2034 will not only be physical but behavioral. Human and machine capabilities will grow together, and humans can further develop the unique capabilities of lateral thinking, creativity, and problem-solving.
It is expected that in the coming decade, production tools and manufacturing 5.0 technologies such as exoskeletons, AR, VR, AI, big data, and digital twins will bring significant value to the industry. With organizations leveraging manufacturing 5.0 technology to optimize resource usage, reduce waste, and build more resilient supply chains, sustainability will also take center stage.
Furthermore, as AI continues to dominate in this new era, there will be a growing emphasis on ethical and responsible AI practices, ensuring fairness, transparency, and accountability in decision-making processes.
In short, the future of Industry 5.0 promises a transformative journey towards intelligent, resilient, human-connected, and sustainable manufacturing ecosystems that empower workers, satisfy customers, and drive economic growth.
So, as this new era unfolds, businesses should opt for reliable software development services to build revolutionary solutions that foster responsible and inclusive manufacturing industry growth.
Ensure a Smooth Transition from Industry 4.0 to Industry 5.0 with Appinventiv
The adoption of Industry 5.0 in manufacturing has a transformative impact on the workforce, enhancing several critical aspects of the working environment while prioritizing collaboration, customization, safety, and sustainability.
As businesses embark on the manufacturing 5.0 journey, it is essential to have a reliable software development services provider by their side. At every step of the way, having a reliable development partner like Appinventiv can make all the difference.
Our team of 1500+ tech professionals carries the core competence in developing cutting-edge solutions tailored to the specific needs of Industry 5.0 manufacturing, helping organizations stay at the forefront of technological innovation.
Together, we can revolutionize the factory floor, creating human-centered, smarter, safer, and more efficient manufacturing environments that benefit workers, businesses, and society as a whole.
Embracing Industry 5.0 manufacturing will indeed lead to a more sustainable, resilient, prosperous, and human-centric future of manufacturing. Partner with a leading manufacturing IT services & solutions provider like us to ensure the smooth adoption of Industrial Revolution 5.0 and automation in the manufacturing industry.
FAQS
Q. What is the impact of Industry 5.0 on the manufacturing industry?
A. The impact of Industry 5.0 in the supply chain and manufacturing industry is profound and transformative. It revolutionizes supply chain and production processes by seamlessly integrating advanced technologies like AI, robotics, and IoT, increasing efficiency, productivity, and quality control.
Furthermore, Industry 5.0 fosters human-machine collaboration, enhancing safety and job satisfaction for workers. Also, 5.0 automation in the manufacturing industry enables mass customization and agile production systems, catering to user preferences and market demands.
In short, Industry 5.0 drives innovation, sustainability, and competitiveness in the business processes, transforming the manufacturing industry into a more intelligent, human-centric, and adaptable ecosystem.
Q. How can businesses gear up for Industry 5.0 in manufacturing?
A. To gear up for Industry 5.0 in manufacturing, companies must adopt some key strategies. Some of the most remarkable steps businesses should take to leverage the maximum advantage of the fifth industrial revolution are:
- Invest in advanced technologies like AI, IoT, and robotics to modernize production processes and enhance efficiency.
- Foster a culture of innovation and continuous learning among employees. It will help them adapt to new technologies and workflows.
- Collaborate with technology partners and tech experts, such as Appinventiv. A reliable tech partner can provide invaluable support in developing tailored solutions and navigating the complexities of Industry 5.0 implementation.
- Embrace sustainability practices and prioritize ethical considerations in technology adoption. It will help ensure responsible and future-proof manufacturing operations.
By following these proactive strategies, companies can effectively gear up for Industry 5.0 and gain competitive advantages in the evolving manufacturing landscape.
Q. What is the major reason to shift to Industry 5.0?
A. The major reason to shift to Industry 5.0 is driven by the urgent need to address pressing global challenges such as environmental degradation, pandemics like COVID-19, and geopolitical wars or conflicts.
These crises have underscored the limitations of traditional industrial models and triggered the importance of redefining industries to prioritize sustainability, resilience, and synergy between humans and smart machines.
Manufacturers recognize that transition to Industry 5.0 is essential to drive innovation, adapt to rapidly changing circumstances, and build a more sustainable and resilient future.
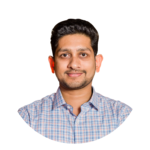
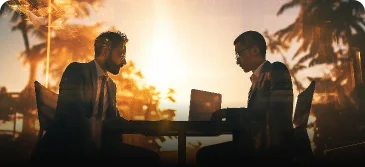
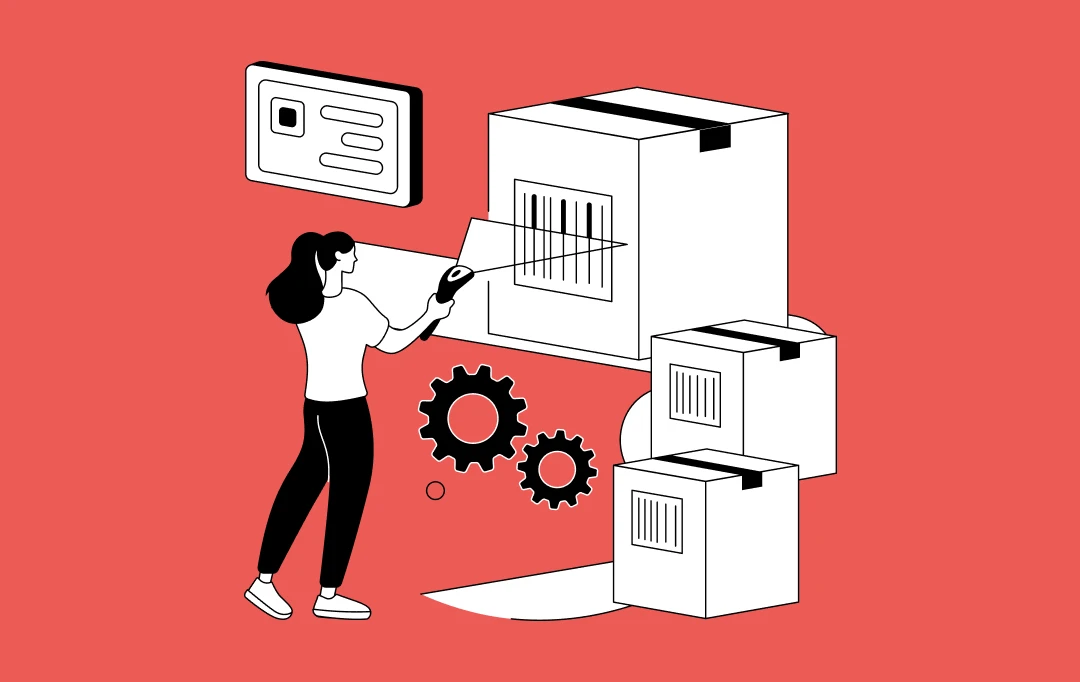
Custom Order Management Software Development - Benefits, Types, Features, Process, Costs
In an increasingly interconnected world, businesses face the constant challenge of meeting diverse customer demands while ensuring seamless operations. As consumer expectations continue to evolve, the need for efficient and tailored solutions becomes ever more pressing. This is where a custom order management system becomes essential, serving as a pivotal tool that is quietly revolutionizing…
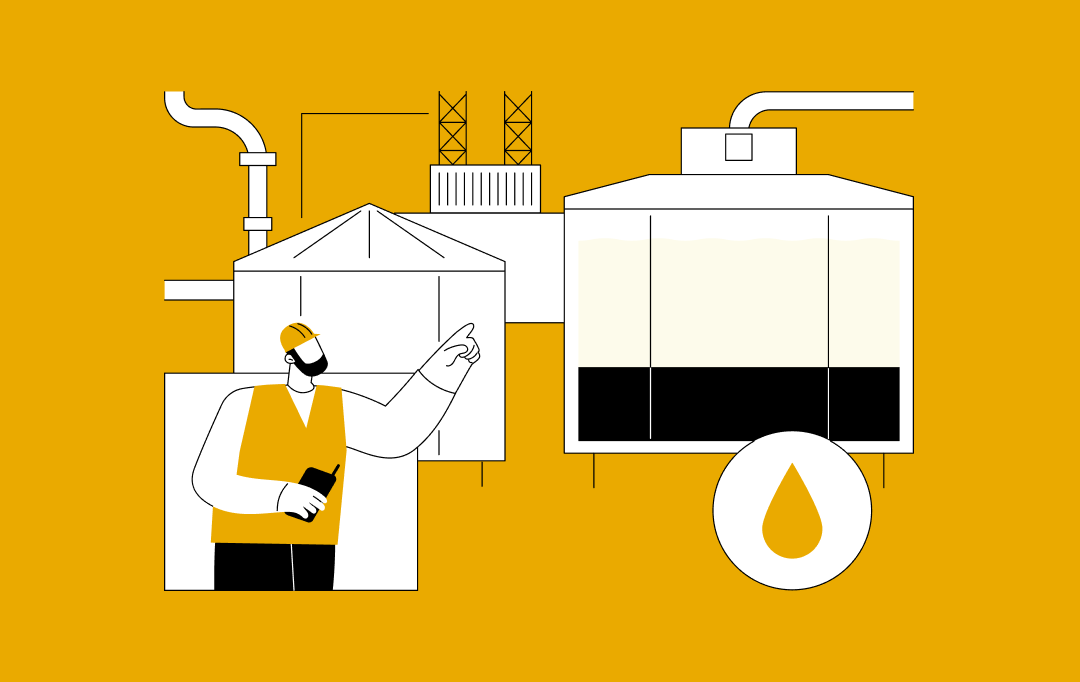
Oil and Gas Field Service Management Software: Process, Benefits, Features, Costs, and More
The oil and gas businesses are witnessing immense transformations in today’s digital landscape, fueled by innovative software solutions and advanced technologies like AI, IoT, and ML. These technological advancements have blurred the line between geographical borders, empowering businesses to scale their operations globally easily. Yet, managing and optimizing oil and gas operations across remote locations…
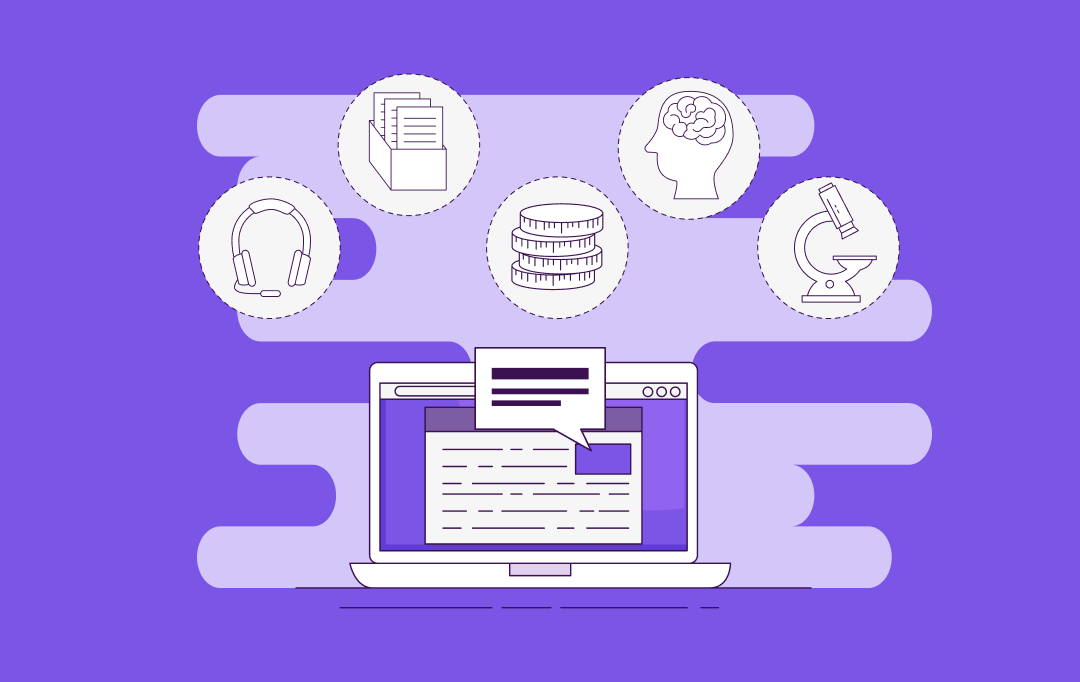